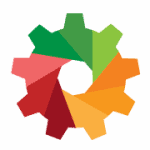
Setting up industrial operations is part of the capital expenditure a business has to undertake. Businesses now analyze the lifetime cost of any capital expenditure before making a decision. This includes the inventory cost, labor expenses, maintenance costs, cost incurred due to expected downtime, and expenses for upgrades. This tilts the decision in favor of options that provide long-term machine reliability and reduced maintenance.