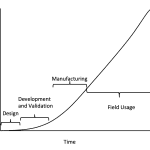
Introduction
Businesses, to be competitive, need to control all costs. Product or service failure can result in large uncontrolled costs. As product development proceeds, the cost of failures increases. The concept is shown in figure 1.
Figure 1
Your Reliability Engineering Professional Development Site
by Dennis Craggs Leave a Comment
Businesses, to be competitive, need to control all costs. Product or service failure can result in large uncontrolled costs. As product development proceeds, the cost of failures increases. The concept is shown in figure 1.
Figure 1
by Robert Allen Leave a Comment
When considering a business process improvement (or some other) initiative, we also want to communicate to motivate the right behaviors. However, initiatives often seem to use buzzwords or use titles familiar to employees that have seen such initiatives come and go (the key word being “go”).
by Robert Allen Leave a Comment
In previous articles we covered design for six sigma and design for lean. Now let’s take a look at Design for Assembly. We’ll do this by following the Design for Six Sigma (DFSS) thought process, and add design for assembly (DFA) subtopics as follows:
by Robert Allen Leave a Comment
When it comes to ensuring a task or deliverable is accomplished, we often see the word “owner” used. Perhaps surprisingly, there really is no true ‘owner’ of anything in the context of program or project management.
We can begin explaining this with two adjectives: responsible and accountable.
In this article series, we covered several topics in the area of product development and project management. We will now begin to explore process improvement with the topic “Design for Lean”. While design for lean may be a subtopic within product development, it helps us understand operational risks, operational costs, enables operational planning and process improvement.
by Robert Allen Leave a Comment
Previous articles have covered product development tools and methodologies such as lean product development, agile, design for six sigma, product life cycle (PLC) and project management processes.
In this article, lets consider “the product” being developed any hardware product, software, IT system, service or new business process. We’ll use the acronym “PSSBP” (Product, Service, Software, Business Process) as an all-encompassing placeholder and to illustrate critical thinking on the topic as follows:
by Robert Allen Leave a Comment
In a previous article, we defined design for six sigma (DFSS) as a thought process focused on maximizing customer value and minimizing cost.
More specifically, DFSS is used to reduce variability in product performance (thereby increasing value), using analytical models and our knowledge of manufacturing variability to enable specification limits on difficult-to-manufacture tolerances to be increased (thereby reducing cost).
by Robert Allen Leave a Comment
For the majority of organizations, long-term success is tied directly to the new product development process. Tomorrow’s revenue and growth are tightly bound to how successful you are at launching new products.
…fewer design iterations to achieve the same goals (reduced time to market), more efficient production and delivery processes (reduced operating costs), fewer defects & warranty costs during the entire product life cycle (increased customer satisfaction).
by Robert Allen Leave a Comment
In this article, we’ll compare and contrast the definition of a requirement, with a ‘story’, which is used in agile/scrum.
The framework for each is somewhat different, however.
Recall the definition of a requirement:
…a requirement defines “what the product (or process) design shall provide <output> at operating conditions <input>”
The framework of a story is as follows:
In this weeks article, we’ll explore how the three disciplines (product development, process improvement and project management) can enable change management.
First, it’s worth reflecting on how these disciplines fit together. Starting with product development our goal is to understand customer value, and to optimize the product (or service) by maximizing customer value and minimizing cost. It can be seen that, process improvement naturally complements this objective as way to further reduce costs. In addition, project management establishes how product development and process improvement is planned, executed, controlled and monitored.
Now let’s look at some key attributes of change management, along with elements of the three disciplines mentioned above.
by Robert Allen Leave a Comment
Lean product development might mean different things to different organizations, but let’s start with the 5 principles of lean manufacturing and see how it can be applied to the product development process. [Read more…]
by Robert Allen Leave a Comment
In recent articles I focused on a ‘linear’ approach to product development by understanding customer needs, establishing requirements (“what the design provides”), establishing a conceptual design, etc.
In this article, I’ll discuss a framework whereby an idea for a product or design might kick-off the process.
Also, rather than a commercialized product, we will assume our goal is to successfully demonstrate the idea’s feasibility. (This is common for a start-up company, where the business model might be to demonstrate product success with a goal of obtaining more venture capital, or to sell the intellectual property. Alternatively, a large company might want a separate idea development process that takes invention off the critical path.)
by Robert Allen Leave a Comment
Wouldn’t it be great if we could require the stock market to provide us 15% increases in our portfolio every year…or if we could simply require a sunny day for a picnic?
You might be familiar with the term ‘market requirements’ or a ‘market requirements document’ as a deliverable in the definition phase of a product life cycle process. To understand why market requirements don’t really exist, we must first provide the definition of a requirement. [Read more…]
by Robert Allen Leave a Comment
A generally accepted principle for a successful business is great people, processes & products. This can be further simplified as “maximizing customer value and minimizing cost” of the product.
Consider the following:
by Fred Schenkelberg Leave a Comment
Reliability engineers are equipped with an arsenal of techniques (FTA, RBD, Markov, FMEA / FMECA, SIL) for reliability, availability, safety and maintainability analysis. However, it is not always clear when to use each technique.
In order to design a safe and reliable product, reliability engineering techniques should be integrated with the system design process. This fact is well known, and today many system engineering conferences include discussions regarding reliability and safety [1,2]. [Read more…]