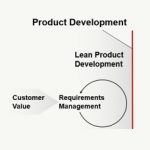
When considering a business process improvement (or some other) initiative, we also want to communicate to motivate the right behaviors. However, initiatives often seem to use buzzwords or use titles familiar to employees that have seen such initiatives come and go (the key word being “go”).