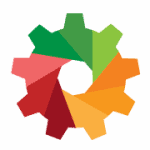
A failure reporting, analysis, and corrective action system (FRACAS) is an important part of a reliability program. It is used to solve reliability and maintenance issues throughout a plant’s lifecycle. It uses a strict closed-end loop and iterative root causes analysis process. Properly executed, it can add considerable value to a business. However, there are some implementation traps to avoid and best practice tips that optimize results; here are six common issues to consider. [Read more…]