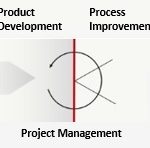
A complex production process requires a mixture of leadership, governance and management. In this article, we’ll discuss a tiered meetings structure that can effectively enable this. Empowerment, escalation paths, accountability and responsibility are included as some key ingredients. We’ll start with the following diagram: