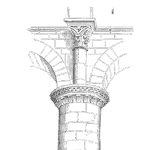
Dr. Taguchi was an engineer, not a statistician. He considered the ability of design of experiments (DOE) to identify and reduce sources of variability, yet needed a system that did not require a statistician to implement.
Dr. Taguchi proposed a few considerations for those applying the Taguchi design of experiments approach.
Quality Definition
Rather than the common quality definition related to meets specification, Dr. Taguchi thought of quality in terms of the minimum loss to society. In engineering terms this translates to consistency of performance. A related principle is the minimization of variation.
Consistency means the process or product performance is close to the target. Creating products that are built on target for each dimension and not simply within the tolerance limits for each dimension performs better thus creating less loss to society.
In order to design and build quality, Taguchi suggests a two step process:
- Determine the factor level combination which minimizes performance variability.
- Adjust the factor levels to achieve on target performance.
Standardized and Simpler DOE
In order to introduce practical designed experiments into industry, Dr. Taguchi limited the experimental arrays to orthogonal arrays. One definition of an orthogonal array is:
The set of experimental treatment combinations that has for each pair of factors that each treatment combination occurs the same number of times across the possible factor levels.
The use of orthogonal arrays is common within design experiments as they are efficient, easy to setup and to analyze.
Robust Design Strategy
The operating environment for any product contains stresses that vary. These external stress are not controllable by design or the product, yet may impact the product or process performance.
Within the design process consider the stresses, the noise factors. Dr. Taguchi’s designed experiment approach includes an outer array design that enables a smaller study size to determine the effects of a large number of noise factors.
Taguchi Loss Function
Briefly described in the article, Taguchi’s 3 Fundamental Concepts, the loss function is a mathematical relationship between performance deviation from the optimal target performance and the cost to society.
One use of the loss function is to quantify the benefits of changes to a design or process to adjust performance to the target. This provides a viable means to estimate the return on investment to make design or process changes.
Signal-To-Noise analysis
Classical DOE analysis often employs analysis of variance techniques. Dr. Taguchi simplified the analysis by using the signal to noise ratio. The approach provides an easy to interpret set of results that help experimenters and designers determine the appropriate set of factor levels that both create a robust system that performs on target.
Summary
This short list include 5 concepts to consider when working to improve the quality or reliability performance of your system. They summarize the basic tenets of Dr. Taguchi’s approach.
To read more about the Taguchi DOE process, check out the two articles:
Planning a Taguchi L4 Array Experiment
And
Analyzing a Taguchi L4 Array Experiment
This short article is based on the work of Ranjit Roy in chapter 1’s brief comparison of classical and Taguche designed experiment approaches.
Roy, R. A Primer on the Taguchi Method, 2nd edition Dearborn, MI: Society of Manufacturing Engineers, 2010.
Leave a Reply