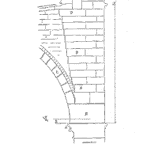
Taguchi may be best known for the variation of design of experiments that bear his name. Yet the impact of his work is felt across the product life cycle and all of the quality field.
Building on Deming’s observations that 85% of poor quality is due to faulty processes and only 15% due to the worker, Taguchi focused on creating robust processes.
A robust system is one that tolerates the daily and seasonal variations of the environment, machine wear, and equipment part-to-part variation, etc. A robust system operating in the range of real world conditions.
Taguchi basic philosophy has three concepts:
- Design quality into the product.
- Achieve quality by minimizing deviation from the target.
- Measure the cost of quality as a function of deviation from the standard (Taguchi loss function).
Let’s explore each of these a bit more.
Design quality into the product
As a brand new manufacturing engineer I was asked to write a letter to a customer explaining why a product they purchased from us failed. My first inclination was the design of the product wasn’t appropriate for their use conditions.
I knew that in manufacturing we could make a product almost as good as the design. In essence we could only make actual products that would not be good quality and reliability wise as the design. We could only make it worse.
A product failure is always the designer fault, was my new mantra.
This is what Taguchi is saying too. The ability of a product to meet your customer’s expectations is fundamentally set by the design. Yes, manufacturing can, and will, create products that are not as good as the design intent, yet that has to be accommodated by the design.
Taguchi firmly believed that quality had to designed into a product. The quality work started with the initial design. Instead of attempting to inspection in quality, ‘in-line’, he recommended the focus on designing a robust product during ‘off-line’ during the design and development phases.
Furthermore, the design of the ‘in-line’ or manufacturing process had to address the quality of the process thus ensuring the creation of quality products.
Achieve quality by minimizing deviation from the target
In the article, Robust Quality, Taguchi and Clausing described the manufacture of vehicle transmissions in the US and Japan to the same set of plans. The Japanese transmissions enjoyed markedly ‘lower production, scrap, rework, and warranty costs.’
The article also describes a more dramatic difference when Sony built televisions in Japan and the US.
In both cases the US team strived to get each unit within specification. The Japanese steams worked to get unit on target. The units that technically met the specification, that were near the tolerance limits, tended to not meet customer quality and reliability expectations. Units with on target assembly were more robust and performed well.
Building to target not within tolerance makes a difference. It improves your ability to efficiently manufacture a product, and customers enjoy a product that meets their expectations.
The Taguchi loss function
Taguchi’s third point is the loss due to an item not being on target can and should be calculated. The study of the relationship between product performance and cost of failures related to how well an item is built to target (not within specification) guides the investments in making improvements.
For example, if the warranty costs double for items made near the tolerance limits versus on target, one could determine an appropriate investment to improve the ability to build to target more often.
The costs include the cost of scrap, rework, inspection, returns, warranty service calls, and replacement systems or subsystems. The loss function concept extends to the cost of failure incurred by the customer, which is difficult to quantify in most cases.
Summary
Taguchi suggests an ongoing and continuous work to improve the design and manufacture of products. The investment to reduce variation about the target has a favorable ROI when considering the aversion of failures and improvements to brand loyalty.
As much as a focus on reducing variation, Taguchi suggests the culture around continuous improvement is key. In spec is not good enough. There is room to improve the design and process to meet customer expectations and eliminate variation.
Hi there,
I am looking for a private tutor to explain to me Taguchi’s Design of Experiments. If you have anyone who can help me, please let me know.
Thanks,
Ali
Hi Ali,
There are plenty of good books out there on the topic. That would be a good place to start. My favorite is by Lloyd W. Condra titled Reliability Improvement with Design of Experiment.
cheers,
Fred