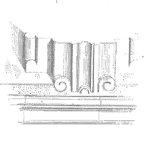
Peck’s Relationship
High temperature & humidity is a common test condition. For specific failure mechanisms, there are models available (or you can create a model) to determine the translation from test to use conditions.
These acceleration models generally only apply to one specific failure mechanisms and do not apply to a system level estimate of life. If the failure mechanism is the dominant failure mechanism for the product, then an ALT exploring just that mechanisms would provide a life estimate.
Peck’s relationship is an acceleration model for the effect of humidity on the metallization elements of integrated circuits within plastic enclosures (typically an epoxy over molding).
Peck’s Relationship for Temperature & Humidity
When electronic components moved from small metal cans to epoxy packaging, one of the issues was moisture ingress leading to the silicon device failing quickly. If the epoxy over-molding did not form an adequate seal the application of a relatively high humidity at an elevated temperature could determine if the package would survive nominal temperature and humidity conditions for an extended time.
Peck and colleagues gathered reports and studies of the effects of temperature and humidity on the time to failure behavior for a range of epoxy based packages. The model they developed is empirically derived from a large number of different life studies.
$$ \large\displaystyle {{t}_{f}}=A{{\left( RH \right)}^{-n}}{{e}^{{}^{{{E}_{a}}}\!\!\diagup\!\!{}_{kT}\;}}$$
Where $- {{t}_{f}}-$ is the time to failure
A is a constant dependent on the materials, process, and conditions
RH is relative humidity
n is a constant
Ea is the activation energy
k is Boltzmann’s constant, 8.617 x 10-5 eV/K
T is temperature in Kelvin
Acceleration Factor or Model
Using Peck’s relationship as a ratio of test conditions over use conditions we are able to eliminate the constant A, it simply cancels out.
$$ \large\displaystyle AF={{\left( \frac{R{{H}_{u}}}{R{{H}_{t}}} \right)}^{-n}}\exp \left[ \frac{{{E}_{a}}}{k}\left( \frac{1}{{{T}_{u}}}-\frac{1}{{{T}_{t}}} \right) \right]$$
The ratio results in the acceleration factor, AF, or the number of times one can multiply the test, subscript t, determined time to failure data to estimate the use condition, subscript u, expected time to failure duration.
Note the model is a form of an Erying model being the product of the inverse power law for humidity and the Arrhenius equation for the temperature elements.
The Constants n and Ea
The constants were determined fitting the data from hundreds of studies using simple regression techniques. The constants vary depending on the:
- Geometry
- Material set
- Process conditions
- Testing conditions
- Use conditions
The values in Peck’s paper and in subsequent papers or books are only a starting point providing a rough model. You should determine the appropriate constants for your particular circumstance when ever possible.
In Peck’s paper he reports n = 2.7 and Ea = 0.79 eV. These values are also listed in Nelson’s discussion of the model.
Wayne Condra discusses Peck’s relationship and uses n = 3 and Ea = 0.9 eV.
Summary
You acceleration factor may differ. Peck’s relationship is a great place to start when evaluating the longevity of moisture induce IC failure with epoxy over molded components. You can improve your acceleration model by determining the fitted constants for your specific system.
Finally, keep in mind Peck’s relationship is an acceleration model for temperature & humidity evaluation of moisture induce IC failure within epoxy over-molded components. It is not a general model for any application of temperature & humidity testing.
Peck, D Stewart. “Comprehensive Model for Humidity Testing Correlation.” Reliability Physics Symposium, 1986. 24th Annual (1986): 44-50.
Nelson, Wayne. Accelerated Testing: Statistical Models, Test Plans, and Data Analysis. Edited by S S Wilks Samuel. Wiley Series in Probability and Mathematical Statistics. New York: John Wiley & Sons, 1990.
Condra, Lloyd W. Reliability Improvement with Design of Experiments. New York: Marcel Dekker, 2001.
Hello, I want to know n – constant, how to derive that plz define it.
In the work that Peck did reviewing hundreds of studies he found n = 2.7… that is an grand average fit. It is a regression analysis with your data at different humidity levels and different temperatures to determine the constants that work for your situation. n = 2.7 is a starting point for planning. The differences in materials and assembly processes will likely change these constants, yet I’ve not seen papers published in this area for some time.
A good starting point to design such an experiment would be to review the papers Peck references in his work.
Cheers,
Fred
Thanks for your reply Mr. fred.
Can you show any proof. Please i need for my study.
The best place for details on the relationship is Peck’s paper
Peck, D Stewart. “Comprehensive Model for Humidity Testing Correlation.” Reliability Physics Symposium, 1986. 24th Annual (1986): 44-50.
Cheers,
Fred
Not sure there is a proof or derivation for the formula – it was empirically fit to hundreds of studies of temperature and humidity testing determining time to failure. Peck used regressional analysis to find the fitting parameters, n and Ea.
how can i find n and a constant for nimonic alloy?
can i use this equation for creep?
Not sure you could find constants for nemonic alloy and no, this equation is not suitable as is for creep. Cheers,
Fred
Hello Fred,
Thank you for such simple yet understandable article.
So, when i have to choose between Lawson model and Peck model, what should i Pick?
I see that in Lawson model, both the humidity and temperature factor are raised to the power of exponential where as it is not in case of Humidity factor in Peck´s model.
Regards,
Raju Nalluri
Hi Raju,
I’m not familiar with Lawson’s model and a quick search found the formula, yet I’ll have to research a bit more to understand what Lawson was modeling – specifically what failure mechanism.
In selecting any model for estimating the acceleration factor the choice is based on how well the model describes the stress to time to failure relationship for a specific failure mechanism. Temperature and humidity excite many different failure mechanisms that likely have different stress/time to failure relationships.
The best way to select a model is after you have failures and can confirm the mechanism at work… without that knowledge, it is engineering judgment.
Cheers,
Fred
Hi Fred
do you think Peck is also can use for plastic material HALT, and what ‘s the Ea and n is suitable
Please forgive me for not being an English user
Hi Mark,
Peck’s equation was developed to fit data concerning the ability of epoxy coatings to seal around lead frames for plastic encapsulated components, like linear amplifiers. The equation may or may not fit other sets of data describing different failure mechanisms – that is something to evaluate.
For a HALT, a highly accelerated life test, done to expose weaknesses within a design, then I do not see the use of any formula suitable for estimate lifetime – the nature of HALT with multiple step-stress factors more of exploration for margins and unexpected failures.
If conducting an accelerated life test designed to estimate the time failure distribution for a specific failure mechanism, then first focus on that failure mechanism when selecting the appropriate acceleration factor equation.
cheers,
Fred
Hi Fred,
Good article… i would like to know what is the unit of time calculated from this model. Is it in second/minutes/Hours?
Please suggest
Karmshil
Hi Karmshil,
you may use whichever units are appropriate for your situation, as long as you are consistent.
cheers,
Fred
Hello Fred Schenkelberg,
Above test applicable for shelf life testing Medical consumable & sensors ? (accelerated aging test )
A high temperature and High humidity together may damage the material property of plastics ? example – Polycarbonate.
Kindly reply
Hi Roopesh,
Each and every ALT has to be detailed for the failure mechanism involved along with all the constraints, such as material characteristics.
Please do not use a generic ALT plan without doing the engineering work to make sure you will end the testing with valid and useful results.
cheers,
Fred
I didn’t know how temperature and humidity testing it’s a must-have for certain mechanisms. In my opinion, it’s important to test a product to identify its features. If I were to invest in an industrial manufacturer, I’d test my products regularly. Thank you for the advice on humidity testing and how it gets done.
What is the relation of using Conservative RH constant (exponent) as 2.66 ≃2.7 or 3 in acceleration factor calculation [A_RH = (RH_field/RH_test)^-n] ?
Is it somewhere related to an average activation energy of the device under test or component under test.
Hi Lokesh,
Thanks for the note and question. Peck determined the constants, the RH exponent and the activation energy Ea empirically. He analyzed hundreds of datasets for temperature/humidity testing and used simple linear regression techniques to derive the constants. If the constants have any physical or chemical relevance that was not discussed in the work, nor part of the analysis.
The constants simply define the best-fit line for the given equation of many sets of temperature/humidity experimental results. Also, keep in mind that these constants only related to experiments conducted on epoxy encapsulated electronica components (mostly ICs. And, those experiments were done decades ago and may or may not apply to today’s technologies.
cheers,
Fred
Hi Fred,
First appreciate your effort to put on this web page.
I found a later paper from Peck,
two things are updated:
First 1986; n = 2.7 and Ea = 0.79 eV.
1991 ; n = -3·0; Ea, ~ 0.9 eV
Second is temperature and humidity range:
1986: 158°C down to 50°C and from 100% RH down to 50 %RH
1991: 158ºC down to 20ºC and from 100 %RH down to 20 %RH
QUALITY AND RELIABILITY ENGINEERING INTERNATIONAL, VOL. 7. 169-180 (1991)
“RECENT HUMIDITY ACCELERATIONS, A BASE FOR, TESTING STANDARDS”
By, ORJAN HALLBERG and D. STEWART PECK
CURRENT DATA
The data used in this current analysis are taken from
publications from 1979 to 1987,7-15. 17-27 using a
total of 87 data points of comparisons of the ratio
Ro of tm (T/RH) to tm (85/85) to the calculated ratio
Rc according to an assumed formula. Data published
before 1979 were not used because they represented
sporadic attempts, frequently on home-made equipment,
and with variable attempts at cleanliness of
equipment or test items. Furthermore, it was recognized
that the chloride content of the epoxy could
be critical, and that later products might be more
useful for future use. This will be discussed later.
Figure 1 shows the plot of all Ro vs Rc, points, as
in Reference 1, but resulting from the range of data
from 158ºC down to 20ºC and from 100 per cent
RH down to 20 per cent RH. The data optimally
fit equation (1) with the following parameters:
n = -3·0; Ea, ~ 0.9 eV
Correlation coefficient: 0.985; Ro intercept: 1.010;
Slope: 0.98
This compares with the earlier correlation coefficient
of’ 0.986 for the 61 data points of 1986 (D. S. Peck, ‘Comprehensive model for humidity testing correlation’,
Proc. lRPS, 1986, pp. 44–50.)
Thanks for the follow up and tracking down the second paper. For this and other equations found in books or online – I find it always useful to read the original paper/work to fully understand how to properly use and interpret the equation.
cheers,
Fred