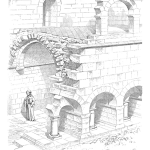
Many people believe Proactive Maintenance is the ultimate physical asset management strategy—but there is one better strategy. To get world class reliability at the least cost there must be no maintenance. Only a “wellness” paradigm can achieve that result.
Keywords: machinery health, equipment reliability, plant and equipment wellness
There is a huge difference in paradigms and practices between proactive maintenance and plant “wellness”. Figure 1 represents the difference between the two. It shows proactive maintenance is an intervention done to a physical asset. Whereas plant wellness is a systematic set of practices used across the life cycle to sustain asset health so no maintenance intervention is required.
When the word “maintenance” is used in relation to physical assets it has a particular meaning. An Internet search provided a definition of maintenance as: the process of preserving a condition or situation or the state of being preserved. The online Merriam-Webster dictionary defined
maintenance as: the act of maintaining | the state of being maintained | Support. It also had a second meaning: the upkeep of property or equipment.[1]
Maintenance is done to a thing when it is no longer fine.
“Proactive” is defined in the online Merriam-Webster dictionary as: acting in anticipation of future problems, needs, or changes.[2] To be proactive is to get ahead of an issue and keep it under control.
The term “proactive maintenance” means “to intervene to sustain an asset in a healthy condition.” You do proactive maintenance on a thing to stop it degrading into an unacceptable state.
The proactive maintenance paradigm mixes intentional preventive and predictive interventions to keep an asset in the condition needed for reliable operation. For example, to have reliable car tyres you keep tyre pressure in the ideal range by regular preventive maintenance every few weeks to add air until the pressure is right. You also regularly check tread depth and damage with predictive maintenance done every few months or thousands of kilometres to establish a degradation rate and estimate when the tyre will need replacement. In this case the combination of preventive and predictive maintenance is proactive maintenance because their use satisfies the proactive paradigm to intentionally keep the conditions needed for reliability. A second example is to check machine shaft alignment with vibration analysis on regular predictive maintenance to confirm alignment is accurate and if necessary reposition the driver and driven assemblies to their ideal spots. Another example is to filter oils in situ to remove solids and wear particles on a regular preventive maintenance cycle, coupled with a predictive maintenance activity of sampling the oil every few months or hundreds of operating hours to check its chemistry and identify changes in composition.
Proactive maintenance is sound asset management strategy and its use will reduce failures, lift reliability and lower maintenance costs. However, there is one other paradigm that trumps proactive maintenance—it is plant and equipment “wellness”.
An online search for the definition of the word wellness provided the following extract related to human wellness[3]:
Wellness is an active process of becoming aware of and making choices toward a healthy and fulfilling life.
“…a state of complete physical, mental, and social well-being, and not merely the absence of disease or infirmity.” – The World Health Organization.
“a conscious, self-directed and evolving process of achieving full potential.” – The National Wellness Institute
Wellness is more than being free from illness, it is a dynamic process of change and growth.
The online Merriam-Webster dictionary gave this definition of wellness:
being in good health especially as an actively sought goal.[4]
Wellness is a holistic life endeavour to create and sustain excellent health so interventions due to ill-health do not arise because you live life in a way that minimises the chance of things going wrong in mind or body.
When a physical asset has wellness it does not need maintenance because there is nothing wrong with it. Creating plant wellness is a more effective paradigm for an organization to adopt than proactive maintenance because it gets you to eliminate the need for maintenance. Plant wellness requires you to take a holistic, life cycle view of an asset and do health creating, health promoting and health sustaining activities throughout its life so that there are no causes of operating failure. Without a failure cause there are no failures and outstanding lifetime reliability becomes the norm.
In the car tyre example, a wellness paradigm leads you to building smooth roads and keeping them clean and maintained. It gets you to teach drivers to accelerate gently not heavily, to take corners smoothly and not wildly, and to stay more toward the middle of the road and away from the edges where hard items, sharp objects and rocks collect. Proper shaft alignment under a wellness paradigm would start with buying equipment without softfoot problems requiring shimming of their feet; base plates and mounting frames would be flat, straight and square to precision standards, as well as being strong and robust against twisting under high operating and start-up loads. The driver and driven assemblies would be installed so that when they were run for production their expansion from temperature rise brought them into precision alignment at operating temperature. Instead of doing vibration condition monitoring to observe for shaft misalignment the preference would be to observe that the operating temperature is always controlled to the right value so there is no out of control expansion of the equipment that moved the shafts out of alignment and caused vibration. It would necessitate that the operation of the equipment was accurately done to a procedure that insured the operating temperature was right and it was kept stable. In an organization that had a wellness paradigm its oils would not be allowed to degrade since the causes of lubricant degradation would be removed. Machines would be brought with moisture extracting desiccant breathers installed on gearboxes as the normal design; the shaft seals would be triple protected against ingress of contaminants; the working parts would be designed, manufactured and precisely installed in ways that caused least stress to their microstructure so parts would not wear; the body structure that parts mounted to would remain ridged so there was negligible distortion under the heaviest operating forces. No pipe stress or other external forces to cause parts distortion would be allowed and the installation contractor would meet and be checked against the company’s precision installation standards.
Human wellness is a way of life where you do the right things at the right times so your mind and body are always fit and healthy. Plant and equipment wellness is an organizational paradigm that naturally and automatically creates phenomenally successful production because you have outstandingly reliable machines and equipment. There will still be some maintenance required, like replacing filters, renewing brake pads, buying new tyres, and other such preventive maintenance actions on items with a defined service life, but it will be the absolute minimum maintenance at the absolutely minimum maintenance cost. All the preventive, predictive, corrective and breakdown maintenance time saved becomes new production uptime, and all the moneys no longer spent on maintenance become new operating fortunes for the organization.
Mike Sondalini
Director www.lifetime-reliability.com
[1] http://www.merriam-webster.com/dictionary/maintenance, accessed 18 September 2015
[2] http://www.merriam-webster.com/dictionary/proactive, accessed 18 September 2015
[3] https://shcs.ucdavis.edu/wellness/, accessed 18 September 2015
[4] http://www.merriam-webster.com/dictionary/wellness, accessed 18 September 2015
Leave a Reply