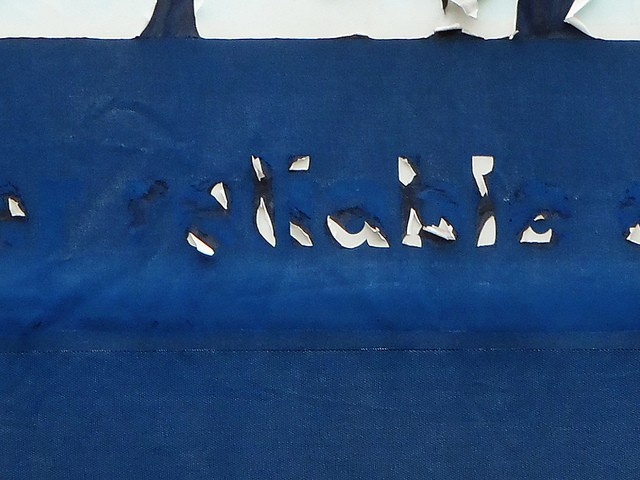
The Fear of
Reliability Statistics

Soon deniable
When reading a report and there is a large complex formula, maybe a derivation, do you just skip over it? Does a phrase, 95% confidence of 98% reliability over 2 years, not help your understanding of the result?
Hypothesis testing, confidence intervals, point estimates, parameters, independent identically distributed, random sample, orthogonal array, …
Did you just shiver a bit?
Or do you know of folks about you that not only do not understand these terms, they do not want to understand.
Signs of Aversion to Statistics
“That result isn’t right.” Actually had this conversation, where presenting results on an experiment to improve factory yield, my boss said that he didn’t believe the conclusion, as it didn’t fit with what he expected. He basically waved his hand over the analysis of measurement error, the data collection procedure, the analysis and conclusions, and said, “Yeah, that’s not right.”
He couldn’t explain it other than he wanted a different result.
“What does this mean?” is an approach that may have two meanings. You did something novel or advanced and your audience truly wants to know more and understand. Said a different way, it may imply they just want to get the overview and just the results — they are not going to sort though the math and analysis to get an understanding.
“I’m off for a weekend in Vegas.” While not a sure sign they do not understand statistics, and it is possible they do enjoy the many entertainment opportunities found in gambling casinos, it may indicate they haven’t grasped the nature of world around them. The law of large numbers requires a lot of numbers before it applies. Just because I’ve lost money on the last 6 trips, that I’m due for a big win, is actually a flawed bit of logic.
We hear that statistics is tough, they didn’t get it in school, or questions about why one sample isn’t enough. We face people that are uninterested, unwilling, or maybe unable to grasp that variance is a measure of dispersion and that shifting the mean about all day long will not help reduce the variability of the results.
It’s not You
Sure many folks, including you would prefer to use a simple easy to calculate value and move on. MTBF is just such a measure, it’s just an average and most of us get that. Beyond just an average, we separate those that ‘get’ statistics and those that don’t.
You are risking confrontation by suggesting that we need to work on reducing the standard deviation, not because it is the right thing to do (how dare you come up with a good idea), it is because you are bordering on topics that your peers do not fully understand.
Learning and master statistical tools takes time and practice for many. And for many they lack the time and interest.
You most likely have taken the time and have found some success with various statistical tools. So, what can you do to continue to make progress improving your product or system?
First, continue to use statistical tools
Second, document and layout the approach, the analysis and the results clearly
Third, find at least one champion that appreciates what you’re doing
Fourth, let the results and benefits speak for themselves (include benefits, results, value created in your reports and presentation — as lower failure rates may go unnoticed otherwise)
Finally, keep looking for ways to apply statistical tools. Get better results and continue to make a difference. Let me know what you have found as resistance to the use of statistics, and what has worked to use statistics to make improvements. What’s working and what’s still a problem? Let’s talk about it.
Fred,
Great article!
The very concept that a reliability engineer would fear statistics is like a lifeguard with a fear of water, or a pilot with a fear of flying.
If a reliability ENGINEER is afraid of statistics, or equations, they really need to find a new line of work, maybe there is an opening at J. C. Penney’s in the shoe department.
Second, your anecdote about your boss not believing your stats is a common phenomenon. The problem is that all the stats we learned in college, Fisherian stats, are notoriously overconservative, not to mention never intended for any decision making.
This very common phenomenon can be avoided by using stats that are intended for decision making, like I outlined in the “What’s all the Fuss” article on noMTBF.com.
Mark Powell
Hi Mark,
Thought you would comment, and thanks for the added note on others believing stats based results.
Part of the solutions is to master and use the appropriate tools, and second is to show the value or benefits. I guess another is to continue to teach and nudge our peers to embrace the nature of variability all about us.
And, I do recommend anyone that hasn’t seen Mark’s article he reference to head on over there and check it out.
What is All the Fuss
Cheers,
Fred
I couldn’t agree more with your comments – if you can’t understand – yes – there are other openings; it’s the key tool; understanding the plant it represents in parallel goes without saying
Fred, the largest resistance is from bottom liners. My definition, bottom liners are interested in only the lowest cost. Quality and Reliability take a back seat to upfront material’s cost. Even when I have presented the data clearly, some getting traction to implement maybe months or years away.
I do not get an hour of their time and being an internal resource, my analysis is largely ignored.
In serveral organizations I have witnessed this behavior. Internal experts are raised up and do good work. Then leaders bring in consultants to train or make a change instead of trusting their own people who have the training and expertise to do the work.
I continually look for opportunities in the problems to get the leaders’ attention.
I am careful to taylor the message because I have found that being too blunt can hurt my own career. Quality is a long road and I’ve learned to be assertive yet patient to find the right timing to deliver the right message.
John,
You have raised the onus of short term costs and long term life cycle costs.
Your “bottom liners” sound like they are focused on short term costs.
Usually, quality and reliability only really start showing advantages in the long term.
So, if the company decision makers are all “bottom liners” and focused on short term costs, quality and reliability will take a back seat.
Mark Powell
Hi John, again thanks for the comment. I suspect that crafting and timing recommendations or proposals is not limited to internal reliability professionals, as many others certainly face the same challenges. cheers, Fred