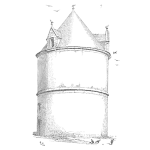
The Instantaneous Cost and Failure from Breakdowns is Huge. When a failure incident occurs, there is a consequential loss of profits and amassing of costs. The cost of failure includes lost profit, the cost of repair, fixed and variable operating costs wasted during the downtime, and a myriad of consequential costs that surge through the business. They are all paid for by the organisation and seen as poor financial performance. The costs of failure cannot be escaped and are counted in fortunes of lost profit per year. Total defect and failure true costs are not normally recognised by managers, yet they can send businesses bankrupt. In the instance of a failure, all its costs and losses are automatically incurred on the business. These costs can only be prevented by not having the failure in the first place. This article explains the ‘Instantaneous Cost of Failure’ (ICOF) and introduces a proactive technique, ‘Defect and Failure True Costing’, that helps companies recognise and prevent this tremendous waste of money.
Keywords: equipment failure, defect cost, operating cost reduction, risk management
The Cost of Failure to a Business
When a business operates it expends fixed and variable costs to make a product which it sells for a profit. Figure 1 is graphical representations of a business in operation. The business produces a product that requires an input of costs which it sells to pay for them and make a profit.
The business has fixed costs that it must carry regardless of how much it produces. These include the cost of building rent, the manager’s salary, the permanent staff and employees’ wages, insurances, equipment leases, etc. There are variable costs as well, such as fuel, power, hire labour, raw materials to make product, etc. From doing business a profit is made that keeps it trading.
We can take the same analogy of normal business operation down to normal equipment operation. When plant and equipment are running each item has a fixed cost, a variable cost and generates a contribution to the overall business profit. It is reasonable to look at every machine and item of plant in your operation as contributing their share to the total profit of the business – their ‘profit contribution’. When an item of plant cannot be used for production, it cannot contribute to profit. If the reason it is not operating is because it has failed, then not only is it not contributing profit, it also imposes added costs on the business.
In Figure 2 a failure incident occurs at time t1 that stops the operation. Several things immediately happen to the business. Future profits are lost because no product can be made (though inventory can still be sold until it is gone). The fixed costs continue accumulating but are now wasted because no product is being produced. Some of the variable costs will fall because they are not used, whereas some, like maintenance, will suddenly rise in response to the incident. Other variable costs are retained in the expectation that the equipment will get back into operation quickly. These are also wasted because they are no longer involved in making saleable product. Usually, workers are put onto other duties they are not meant to be doing. Losses and wastes continue until the plant is back in operation at time t2. The cost for repair from a severe outage can be many times the profit made in the same period (the dotted outline in Figure 2).
If it escalates managers from several departments get involved – production, maintenance, sales, despatch, finance – wanting to know what is being done to fix the stoppage. Meetings are held formally in meeting rooms and impromptu in corridors. Parts are purchased and specialists may be brought in. Customers do not get deliveries and liability clauses may be invoked. Word can spread that the company does not meet its schedules and future business is lost. A rushed work-around is developed that puts people at higher risk of injury. Items are brought, men are moved, materials and equipment are transported to get production going. Time and money better used on business-building activities is drawn into the ‘black hole of failure’.
On and upward the costs build, and on and on people throughout the company waste time because of the failure. The company pays for all of it from its profits, which is then reflected in poor financial performance. The reactive costs and the resulting wastes start immediately upon failure and continue until the last cent is paid on the final invoice. Some consequential costs may continue for years after.
These lost and wasted money can be considered as the ‘instantaneous cost of failure’ or ‘instantaneous loss’. They are instantaneous because as soon as a failure happens, they will need to be spent. There is no alternative but to spend them to get the business back into production. The moneys spent to fix the problem, the lost income from no production, the payment of unproductive labour, the handling of the company-wide disruptions and the loss of future business is money lost forever. However, they would not have had to be spent if the failure had not happened!
The money to fix failures and to carry wasted costs is paid by the business from profits. This explains why having many failures, or a few big failures close in time, it can cause a business to become unprofitable. Figure 3 shows the situation of a business suffering repeated failures (the failures do not need to be equipment failures). The losses and wasted costs accumulate in production, the cost of maintenance climbs, the knock-on costs and wasted time across the business rise and profits in the business fall.
Total and True Instantaneous Failure Cost and Defect Cost
Each organisation is different and each defect, error, and failure it suffers has different consequences. The total cost to the organisation of an incident will be shared amongst the departments and people involved. The proportion of the cost each department ends up carrying depends on the extent of its involvement.
The total and true costs incurred by a business from a failure event reverberate and surge throughout the organisation. The more than 65 consequential costs listed below reflect a good number of them, though there are others specific to each organisation and you will need to identify and record them.
- Labour: both direct and indirect operators
- repairers
- supervisory
- management
- engineering
- overtime/penalty rates
- Product wastescrap
- replacement production
- clean-up
- reprocessing
- lost production
- lost spot sales
- off-site storage
- Services emergency hire
- sub-contractors
- travelling
- consultants
- utility repairs
- temporary accommodation
- Materials
- replacement parts
- fabricated parts
- materials
- welding consumables
- workshop hire
- shipping
- storage
- space
- handling
- disposal
- design changes
- inventory replenishment
- quality control
- Equipment
- OEM
- energy waste
- shutdown
- handover
- start-up
- inefficiencies
- emergency hire
- damaged items
- Capital
- replacement equipment
- new insurance spares
- buildings and storage
- asset write-off
- Consequential
- penalty payments
- lost future sales
- legal fees
- loss of future contracts
- environmental clean-up
- death and injury
- safety rectification
- Administration
- Documents and reports
- purchase orders
- meetings
- meeting rooms
- stationary
- planning, schedule changes
- investigations and audits
- invoicing and matching
- Curtailed Equipment Lives
- Life wasted in previously replaced parts
- Labour wasted in replacing those parts
- Safety Accidents with Equipment
- during maintenance
- during operation
- Quality affected by failure
- defective product
- labour wasted
- other quality costs
The sum totals of the organisation-wide instantaneous costs of failure are not usually considered when the cost of a failure incident is determined. This means that most companies do not fully appreciate the huge consequential costs they incur from every failure incident. Few companies would cost the time spent by the accounts clerk in matching invoices to purchase orders raised because of a failure. But the truth is the clerk would not be doing the work if there had been no failure. The cost was incurred only because the failure happened.
The same logic applies for all the costs due to a failure – if there had been no failure there would have been no costs and no waste. Prevent failures and you will make a lot more money from throughout the business because there was no failure to take the money in the first place.
The full cost of all ‘instantaneous losses’ from a failure incident can be calculated in a spreadsheet. Simply trace all the departments and people affected by an incident, identify all the expenditures and costs incurred throughout the company, determine the fixed and variable costs wasted, discover the consequential costs, find-out the profit from sales lost and tally them all up. It will astound people when you show them how much money was destroyed by one small equipment failure.
It is not important to know how many times a failure incident happens to justify calculating the instantaneous cost of failure. It is only important to ask what the cost would be if it did happen. An extraordinary example was when a 150-mm diameter PVC pipe carrying softened, demineralised water for a major power station failed at a glued joint and began starving the water supply for three boilers supplying steam to six steam turbines. It was only by supplementing the water supply with raw mains water that the power plant remained in operation until the failure was repaired.
Had the failure progressed to its disastrous conclusion an entire city of 1.5 million people, and its industry, would have lost power as each turbine progressively stopped from loss of steam. The repair of the pipe was done for several thousand dollars, but the consequence of the failure was in the hundreds of millions of dollars. Had the instantaneous cost of failure been calculated first, far greater precautions would have been put into place to control the hidden risks inherent in the job.
Preventing the Consequences of Failure
It only needs a few large catastrophes close together in time or many smaller problems occurring regularly to destroy an organisation’s profitability.
By finding the Defect and Failure True/Total Cost (DAFT Costs) of defects and failures you highlight to everyone that many risks to the business previously considered minor are high and they require a strong proactive management plan be put into place to address those risks. The frequency of occurrence maybe low but the cost consequences are massive and so the real risk for the organisation is high (risk = consequence x frequency).
DAFT Costing provides a means to rate the consequences of decisions and failure incidents using real money. The cost outcomes can be clearly and truly identified and priced. Those that are unfavourable can be analysed and modified to reduce the risk. This means the methodology can be used to analyse its consequences and associated costs before a decision is made. The DAFT Costs are tallied in a spreadsheet like the ones shown at the end of the article.
Because DAFT Cost is a means to indicate the real costs of knock-on consequences from a decision it can be used to make good decisions in any situation where understanding the right financial consequences are critical to its success.
Conclusion
Identifying total defect cost and failure cost using ‘Instantaneous Cost of Failure’ shows how vast amounts of money are wasted throughout an organisation when a failure happens. The bigger the failure, or the more often one happens; the more resources and money are lost. The profits that could have been made are gone, wasted, and they can never be recouped.
The next time your operation has a failure do an ICOF on it – what did it really cost your company? If someone designs or selects equipment, ask them for its ‘instantaneous cost of failure’? Ask them what
is its ‘instantaneous cost of maintenance’? What are the cost consequences to the profitability of the business from its failure?
It is critical to your company’s profitability that failures are prevented. Failures can be stopped when companies understand the size of the losses and introduce systems, training, and behaviours to prevent them. The ‘instantaneous cost of failure’ method shows people the instantaneous losses from failure, and the great profit in doing the right things rightly.
Mike Sondalini www.plant-wellness -way.com
Defect and Failure Costing Spreadsheets
(With thanks to www.BIN95.com for use of the spreadsheets)
Leave a Reply