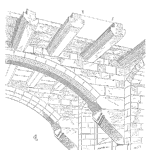
A reliability block diagram is a graphical and statistical representation of the reliability structure of a system.
Graphical as an RBD is drawn with blocks for each element of a system and connecting lines representing the relationship between elements.
Statistical as an RBD also contains the probability of success (reliability) information for each block. For a single point in time, say the warranty period, the probability may be a single number. The probability of success could also be reliability function based on a distribution or non-parametric model.
Let’s consider a simple series system and its RBD. Say the system has three elements, A, B, and C, and if any one element fails the system fails. Thus if A or B or C fail, the system fails. Given this structure we can multiply the individual reliability together to estimate the system reliability, assuming the elements probability of failure is independent.
$$ \displaystyle\large P\left( A \right)\bigcup P\left( B \right)\bigcup P\left( C \right)\Rightarrow R\left( A \right)R\left( B \right)R\left( C \right)={{R}_{system}}$$
This implies that whichever element is most likely to fail limits the overall system reliability. Let’s say element A is at 80% reliability and the other two elements are both at 90% reliable at one year. The system reliability in this case is 0.8 x 0.9 x 0.9 = 0.648 or 64.8% reliable at one year. The system reliability of a series system will always be less than the least reliable element.
Most reliability books and sites online have more details on creating RBDs.
Improvement Strategy
Product development teams have limited resources.
Given limits of money, time, etc. Where should the team invest to improve the system reliability? Let’s explore two options. First, let’s improve element A, the least reliable, from 80% to 85%. Second, consider improving element B from 90% to 95%.
In the first case the system reliability changes from 64.8% to 0.85 x 0.90 x 0.90 = 0.6885, just a little more than 4% improvement. In the second case the system reliability changes from 64.8% to 0.80 x 0.95 x 0.90 = 0.684 or 68.4% which is a little less than a 4% improvement. If the cost of improvements is the same in both cases we would benefit the most by improving the least reliable element.
Another consideration, no matter how much the elements B and C improve the system reliability will not be more than the lowest element’s reliability. Even if B and C have perfect reliability, 1, the system reliability will be 0.85 x 1.0 x 1.0 = 0.85.
Improving the weakest element provides the best opportunity for system reliability improvements in most cases.
The Power of RBD
RBDs are just models and alone have very little utility. Customers will not buy the RBD, but they will buy your product if it’s reliable. So, how should you make use of the RBD to meet your customers and business objectives?
The benefit of an RBD is it encourages two things to occur:
First, it encourages identification and improvement of the weakest element of a system. Second, it encourages improvements in the reliability estimates used for the model.
Both benefits focus the team on improving the product both by taking action to improve the weakest elements and to improve the accuracy of reliability estimates. If the RBD does nothing other than providing a common focal point for the team to discuss system reliability, then it has served some use.
Reliability occurs at the point of decision.
Improving the team’s ability to make a good decision concerning reliability is one of the primary goals of any reliability program. The RBD tool provides a common place to compare the reliability of a system’s elements. It provides a platform for cost/benefit trade-off considerations. It provides a framework to determine the allocation of resources. Even a simple RBD enables the team to discuss reliability in a meaningful manner.
Leave a Reply