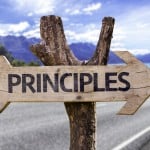
Actions Speak Louder than Words
Consider these questions: How many recommendations are needed to address the root cause of a high-risk problem? If the FMEA team is addressing an issue with high-severity and high-occurrence ratings, is it usual to have a single recommended action to reduce risk? Why not? Read on, to learn the essential elements of FMEA recommended actions, and answers to this questions.
“I have been impressed with the urgency of doing. Knowing is not enough; we must apply. Being willing is not enough; we must do.”
Leonardo da Vinci
Definition of “action”
The Oxford English dictionary defines “action” as “the fact or process of doing something, typically to achieve an aim.”
What is the definition of “Recommended Action” in an FMEA?
“Recommended Actions” are the tasks recommended by the FMEA team that can be performed to reduce or eliminate the risk associated with potential cause of failure. Recommended Actions should consider the existing controls, the relative importance (prioritization) of the issue, and the cost and effectiveness of the corrective action. There can be many recommended actions for each cause.
How are Recommended Actions identified in FMEAs?
The FMEA team reviews each of the high severities (regardless of RPN value), followed by each of the high RPNs, and develops the recommended actions that, when executed, will reduce risk to an acceptable level. There is often more than one action needed to address risk associated with each of the failure modes and causes. The FMEA team should take care to recommend feasible and effective actions that will fully address the risk associated with each failure mode/cause. Whatever action the FMEA team believes needs to be done to address risk must show up in the recommended action column.
In identifying recommended actions, the FMEA team should consider existing controls, the relative importance (prioritization) of the issues, as well as the cost and effectiveness of corrective actions.
For each recommended action, the FMEA team should assign the person responsible, the due date, and other typical project management type of information in order to be able to execute the actions efficiently.
Why is it usually necessary to use multiple recommendations to address high risk? Because, some actions can reduce severity risk, other actions can reduce occurrence risk, and even other actions can reduce detection risk.
What is an example of a Design FMEA recommended action?
Item: Power steering pump
Function: Delivers hydraulic power for steering by transforming oil pressure at inlet ([xx] psi) into higher oil pressure at outlet [yy] psi during engine idle speed
Failure Mode: Inadequate outlet pressure (less than [yy] psi)
Effect (Local: Pump): Low pressure fluid goes to steering gear
Effect (Next level: Steering Subsystem): Increased friction at steering gear
Effect (End user): Increased steering effort with potential accident during steering maneuvers
Cause: Fluid incorrectly specified (viscosity too low)
Prevention Control: Design guidelines for hydraulic fluid selection
Detection Control: Vehicle durability testing #123
Recommended Action: Increase fluid viscosity to standard #xyz
Poorly worded example of Recommended Action: Change fluid viscosity
What is an example of a Process FMEA recommended action?
Process Step: Induction harden shafts using induction hardening machine
Function: Induction harden shafts using induction-hardening machine ABC, with minimum hardness Brinell Hardness Number (BHN) “X”, according to specification #123.
Failure Mode: Shaft hardness less than BHN “X”
Effect (In plant): 100% scrap
Effect (End user): Shaft fractures with complete loss of performance
Effect (Assembly): Not noticeable during assembly
Cause: Induction machine electrical voltage/current settings incorrect for part number
Prevention Control: Shaft hardening setup instructions
Detection Control: audit of shaft hardness
Recommended Action: Install machine alert light (red) to let operator know when voltage or current is set too high
Recommended Action: Implement Statistical Process Control (SPC) charts on machine voltage and current
Poorly worded example of Recommended Action: Implement Statistical Process Control
Application Tips
- In addition to identifying recommended actions to improve designs and reduce risk, the team should review the corresponding engineering or manufacturing requirements. The question needs to be asked, “Do the engineering or manufacturing requirements need to be changed to reflect the design or process improvement?” If the answer to this question is “yes,” the team needs to add recommended actions to improve the requirements. This is important because it is ultimately the engineering or manufacturing requirements that drive product designs, product testing, manufacturing processes and process control plans.
- For high-risk issues, the FMEA team should consider three approaches. First, try to reduce severity risk, if possible. Second, recommend actions to reduce occurrence risk and ensure the actions “fix” the cause. Recall the cause in an FMEA is a design or manufacturing deficiency, as covered in “Understanding FMEA Causes – Part 1.” Third, the team can consider actions to reduce detection risk. Future “Inside FMEA” articles will focus on strategies to reduce severity, occurrence and detection risk.
Next Article
Consider the recommended action “Review results of XYZ test to confirm requirements are achieved.” Is this a good FMEA recommended action to address a high-risk issue? Is it sufficient? Challenge your FMEA knowledge by solving this problem and other problems in the next article.
when Action to be taken in FMEA.
Hi Sandy,
Thanks for your question about when to take action in an FMEA. That is an important question. Let’s take a look at the paragraph titled “How are Recommended Actions identified in FMEAs?”, in the article “Understanding FMEA Recommended Actions.” Here’s what it says.
“The FMEA team reviews each of the high severities (regardless of RPN value), followed by each of the high RPNs, and develops the recommended actions that, when executed, will reduce risk to an acceptable level. There is often more than one action needed to address risk associated with each of the failure modes and causes. The FMEA team should take care to recommend feasible and effective actions that will fully address the risk associated with each failure mode/cause. Whatever action the FMEA team believes needs to be done to address risk must show up in the recommended action column.
“In identifying recommended actions, the FMEA team should consider existing controls, the relative importance (prioritization) of the issues, as well as the cost and effectiveness of corrective actions.
“For each recommended action, the FMEA team should assign the person responsible, the due date, and other typical project management type of information in order to be able to execute the actions efficiently.”
Please let me know if the verbiage in this paragraph answers your question. And do not hesitate to ask further questions.
Carl
IN the PFMEA, once the recommened action has been completed, do you go back and redo the portion of the FMEA with the new RPN? and remove it from the “Recommended action column?
Good question!
In most FMEA standards and company applications, the FMEA Recommendations are executed and the final SOD are assessed. If the SOD risk is not acceptable, the FMEA team can recommend further actions until the risk is reduced to an acceptable level. It is not usually the practice to modify the original FMEA to reflect the design or process modifications or RPNs, during the product development process. Once the FMEA is completed with risk reduced to an acceptable level, the new information can be entered into a generic FMEA, so that future FMEAs will benefit from the updated information. One of the reasons for this practice as described is that FMEAs are legal records showing the due diligence to address risk. I would suggest maintaining the FMEA by version control. If the company wants to initiate a new version of the FMEA, which builds on the previous version, that can be done.
High RPN? When a RPN should be consider as high?