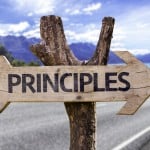
Prioritizing risk for corrective actions in an FMEA – Know before you go!
One of the most important steps in FMEA procedure is prioritizing risk for corrective actions. As soon as Severity, Occurrence, and Detection ratings have been determined for each failure mode and associated cause, the next step in an FMEA is to prioritize the risk and identify which issues need corrective actions. This step has been misapplied more often than any other step in the FMEA process.
“The perfect is the enemy of the good.”
Voltaire
Dictionary definition of “risk” and “priority”
The Merriam-Webster dictionary defines “risk” as “possibility of loss or injury” and “priority” as “superiority in rank, position, or privilege.”
How can the FMEA team prioritize issues for corrective action?
When it comes to prioritizing risk within an FMEA, with the purpose of establishing corrective actions, there are a couple of different approaches to consider.
If company policy or customer mandates a particular approach, such as RPN, of course that approach will need to be used. If there is no policy or mandate, then the following options can be considered.
The initial focus of the FMEA team should be focused on Effects with the highest Severity rankings. If the team is using a 1-10 scale, this means they need to place the highest priority on addressing Severity 9s and 10s. It is essential that the team ensure that the risk associated with high-severity issues is addressed through existing design controls or recommended actions.
Once all of the high-severity issues have been addressed, the team should determine the action priority of other issues in the FMEA. There are two primary techniques that can be used: RPN and Action Priority matrices or tables.
Using RPN to prioritize risk in an FMEA
In an FMEA, Risk Priority Number (RPN) is a numerical ranking of the risk of each potential failure mode/cause, made up of the arithmetic product of the three elements: severity of the effect, likelihood of occurrence of the cause, and likelihood of detection of the cause.
Once all high-severity issue have been addressed, the FMEA team can take up high RPN issues, in sequence.
RPN thresholds are not advised. It is enticing for management to use thresholds for RPN values and require defined action if the RPN value exceeds the given threshold. In most cases, this is a flawed approach, as it can easily become a numbers game. If management exerts sufficient pressure, through excessive consequences for RPN values exceeding thresholds, the FMEA teams or suppliers can bias the RPN components (S, O, and D) to lower the resulting RPN below the threshold. If RPN thresholds are used at all, they should only trigger a heightened level of review, not specifically mandated action.
The FMEA team can develop and implement Recommended Actions to reduce the risk associated with high-RPN issues.
What is an example of a Design FMEA RPN?
[In this fictitious example, the RPN is the numerical product of the severity, occurrence and detection rankings in one line of a Steering Pump DFMEA.]
Item: Power steering pump
Function: Delivers hydraulic power for steering by transforming oil pressure at inlet ([xx] psi) into higher oil pressure at outlet [yy] psi during engine idle speed
Failure Mode: Inadequate outlet pressure (less than [yy] psi)
Effect (Local: Pump): Low pressure fluid goes to steering gear
Effect (Next level: Steering Subsystem): Increased friction at steering gear
Effect (End user): Increased steering effort with potential accident during steering maneuvers
Severity: 10
Cause: Fluid incorrectly specified (viscosity too low)
Occurrence: 5
Prevention Control: Design guidelines for hydraulic fluid selection
Detection Control: Vehicle durability testing #123
Detection: 4
RPN: 200
What is an example of a Process FMEA RPN?
[In this fictitious example, the RPN is the numerical product of the severity, occurrence and detection rankings for one line of an induction hardening operation.]
Process Step: Induction harden shafts using induction hardening machine
Function: Induction harden shafts using induction-hardening machine ABC, with minimum hardness Brinell Hardness Number (BHN) “X”, according to specification #123.
Failure Mode: Shaft hardness less than BHN “X”
Effect (In plant): 100% scrap
Effect (End user): Shaft fractures with complete loss of performance
Effect (Assembly): Not noticeable during assembly
Severity: (Customer Effect): 8 (loss of primary function)
Severity: (Mfg/Assy Effect): 8 (major disruption)
Cause: Induction machine electrical voltage/current settings incorrect for part number
Occurrence: 3
Prevention Control: Shaft hardening setup instructions
Detection Control: audit of shaft hardness
Detection: 7
RPN: 168
Prioritization example using RPN
The following example is a truncated DFMEA on a bicycle brake cable. See if you can identify the risk priority. Which issue is addressed first and second?
Figure 1 – risk prioritization
The first issue to address is the severity 10, RPN 200. The second issue is the severity 10, RPN 40.
Use of Risk Matrices or Action Priority tables in prioritizing risk in an FMEA
The concept of risk matrices or action priority tables is to examine the various combinations of Severity, Occurrence and/or Detection.
For example, it can be useful to graphically display the risk associated with severity and occurrence. The team can plot the combinations of severity and occurrence on a matrix and take corresponding action. This graphical depiction is called a criticality matrix. The criticality matrix identifies severity on the horizontal axis and occurrence on the vertical axis.
See the illustration below, which shows a criticality matrix for a bicycle brake pad. In this example, the team used a severity scale from I to IV, and an Occurrence scale from A to E.
In an Action Priority table, the various combinations of S, O and D can be assigned high, medium and low risk to prioritize actions in an FMEA. The rationale with Action Priority table is that there is no single value, such as RPN, which can prioritize risk in an FMEA. Rather the various combinations of S, O, and D drive the priority. The Action Priority table is company specific, and not “one size fits all.”
Application Tip
Tip # 1:
When assessing the degree of risk using the FMEA ranking scales, it is not appropriate to compare the ratings of one team’s FMEA with the ratings from another team. Even if the product or process appears to be similar, each application is unique in terms of operating environment, customer usage, and specific technical content. The risk ranking scales, including RPN, are designed as a means to prioritize issues for corrective actions within the scope of individual FMEAs.
Tip # 2:
The FMEA team should review and address all high-severity issues first, regardless of RPN value. Once high-severity issues are addressed, the team can review high-RPN issues, and prioritize for corrective actions.
Next Article
In next week’s problems and solutions article, the intermediate problem challenges readers to prioritize a series of RPNs (with their corresponding S, O, and D). In the advanced problem, readers are asked to weigh in on a fictitious debate between advocates of traditional RPN, and advocates of criticality assessment, using only severity and occurrence.
Quality and reliability will be the best if the ‘Top Management ‘ takes it as their responsibility. Then it is every one’s responsibility.
Hello Jayasheel,
Thanks for your comment. I completely agree. When I teach or consult on FMEA, I always advise obtaining management support for implementation of the FMEA process, and bringing high-risk issues from the FMEA to management for their buy-in and support. Same with reliability management. I begin with management and get their support for the entire reliability planning process, from beginning to end. Otherwise the reliability engineer is “pushing on a rope.”