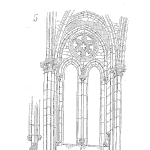
Pressure vessels must be regularly inspected and be maintained in a safe operating condition.
New Australian laws stipulate that all pressure vessels must have a Hazard Level rating (‘A’ highest to ‘E’ lowest) which reflects the vessel’s safety risk (see AS3920.1).
The higher the risk the more stringent the requirements for operating and inspecting the vessel.
Keywords: receiver, non-destructive testing, internal inspection.
What’s a pressure vessel?
The definition of a pressure vessel in Australian Standard AS 3873 is “ a vessel subject to internal or external pressure.
It includes interconnecting parts and components, valves, gauges and other fittings up to the first point of connection to connecting piping.”
Pressure vessels are such things as compressed air receivers (see the drawing below), barbecue gas bottles, steam boilers, aerosol cans, vertical leaf filters, beer bottles, cigarette lighters and fire extinguishers.
This article discusses the general requirements for inspection of unfired pressure vessels such as compressed air and liquefied gas receivers and process reactors.
The other types of vessels are inspected to different criteria.
Why inspect pressure vessels?
It is necessary to inspect the integrity of pressure vessels.
(a) Gases and liquids stored under pressure inside a container are in an energized and compressed state. Rupture of the vessel would result in a catastrophic release of pressure.
(b) The chemicals within the pressure vessel may be toxic (e.g. chlorine and ammonia gases).
(c) The contents may attack, erode, corrode, induce stress, change the metal characteristics or weaken the containment vessel over a period of time.
(d) External impact or corrosion may weaken the pressure vessel. (A real problem with externally insulated vessels where the insulation gets wet from rain or from the process.)
Extent of inspections
Inspections can be in-service inspections where the inspector does an external inspection, tests the pressure relief device operation and does documentation review so he can certify the vessel for continued use for a short period of time.
Or the inspection can be a full inspection requiring inspection of the vessel internal walls and attachments, the external surfaces and attachments, pressure gauges, pressure relief devices, the immediate surrounds of the vessel and documentation.
It may be necessary to remove sections of insulation to expose the outer shell wallIf full visual inspections are impossible or costly it may be possible to substitute nondestructive testing (NDT) methods to confirm the vessel integrity.
Such NDT methods as ultrasonic thickness testing, eddy current thickness testing, acoustic crack detection, magnetic particle crack detection and hydrostatic pressure tests are all viable means of proving vessel integrity.
If full visual inspections are impossible or costly it may be possible to substitute nondestructive testing (NDT) methods to confirm the vessel integrity.
Such NDT methods as ultrasonic thickness testing, eddy current thickness testing, acoustic crack detection, magnetic particle crack detection and hydrostatic pressure tests are all viable means of proving vessel integrity.
What the inspector looks for
Only persons experienced and trained in the techniques of pressure vessel inspections are allowed to conduct the inspection.
Normally a competent, independent third party is used.
The inspector may require improvements to ensure compliance with relevant codes of practice. He provides a written report on his findings and certifies the vessel for continued use for a specific period of time.
The inspector also advises the relevant government department of the condition of the vessel and the due date for the next inspection.
When the certificate is received it is normally displayed in a prominent place near the vessel as proof the vessel complies with the law.
The inspector looks for the following evidence of performance and compliance depending on the Hazard Level of the vessel.
He looks for signs of shell wall thinning. |
He inspects for cracks at welds and at connections to the vessel walls caused by stresses. |
He checks for damage to the shell by impact. |
He looks for leaking gaskets and seals and other evidence of poor maintenance practices. |
He inspects protective coatings and linings to ensure they are in good condition. |
He inspects the soundness of foundations and supports. |
He will want to see the pressure relief device work properly and ensure it relieves pressure build-up. |
He will check the pressure gauge calibration. |
He inspects the immediate vicinity of the vessel for potential risks to the vessel. |
He will look at the relief piping to ensure it vents to a safe place safely. |
He will ask to see evidence of vessel registration with the governing authority. |
He will want to see where the registration is displayed. |
He will look on the vessel for the registration number. |
He will want proof that the design of the vessel is registered with the governing authority. |
He may want to see verified design drawings and calculations. |
He may want to see the manufacturer’s fabrication and materials report. |
He may want to see as-built installation drawings. |
He may want to see the vessel designer’s hazard identification and risk assessment. |
He may want to see proof of the hydrostatic test and other testing performed by the manufacturer. |
He may want to see the installation, commissioning and maintenance instructions from the manufacturer. |
He may want to see the commissioning compliance statement, especially on new installations. |
He may want to see records of inspections, servicing, and maintenance. |
He may want to see the operating log showing records of operating conditions for plant of Hazard Level ‘A’. |
He may want to see records of any in-service inspections or special tests such as proof of instrumentation calibration. |
Mike Sondalini – Maintenance Engineer
DISCLAIMER: Because the authors, publisher, and resellers do not know the context in which the information presented in the articles is to be used, they accept no responsibility for the consequences of using the information.
We (Accendo Reliability) published this article with the kind permission of Feed Forward Publishing, a subsidiary of BIN95.com
Web: trade-school.education
E-mail: info@trade-school.education
If you found this interesting you may like the ebook Centrifugal Pump Problems & Answers.
Thank you for talking about how it is important to inspect pressurized vessels to make sure they do not release toxic gases if they carry any by exploding. It is important to remember that having pressure vessels properly services can help you avoid costly damages and make sure you avoid accidents as well. Personally, I would want to check with the BBB and make sure I find a reputable company that can help me keep my pressure tanks out of danger.