How Bill of Materials (BOMs) Can Exponentially Increase the Efficiency of Your Maintenance Planner
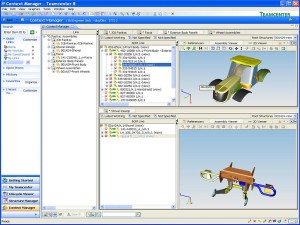
Imagine a world where the Maintenance Planner can quickly and easier find all the material information for each job. Even those that do not yet have a job plan. Dreams or reality? Reality. This reality is found within operations all over the world and you can have it too. How can you achieve a level of efficiency with your Planner and have all materials information readily available? With Bills of Material.
A Bill of Material or BOM as it is commonly referred to, is a list of material needed to support the operations and maintenance of an asset or component. It includes a part description, part number and how many are required on a specific component or assembly. It may also include a reference number that refers to a sub assembly drawing.
Types of BOMs
There are two primary types of BOMs, and the only difference is whether the BOM is built off a piece of Equipment or a Material component. Each BOM has the materials as part of a larger assembly, in an Equipment BOM, all the materials directly to the equipment. In a Material BOM, all materials are attached to the parent material, which may then be attached to the equipment. Figure 1 highlights the differences between them.
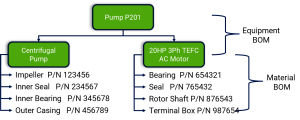
When viewing BOMs, most are setup as a hybrid, with a piece of equipment with many material BOMs attached to it. This is exactly how the example in figure 1 is setup. I recommend this hybrid approach as it allows all the materials to be grouped in logical sub-assemblies, which make the BOM easy to use. Some organizations have used nothing but equipment BOMs, while simple to setup, leads to lists of excess of 200 parts. This is difficult and time consuming to work through.
Why BOMs Are Important
BOMs enable an organization to dramatically increase the speed in which materials can be identified. If the BOM is setup in the CMMS, you can include purchasing information, which greatly increases the speed at which it can be ordered.
As a craftsman, a BOM will facilitate quick and easy identification of a part for retrieval from the storeroom or for ordering. As a maintenance supervisor, the BOM can be used to support the craftsman, planner and the storeroom.
The Storeroom and the Planner are the two functional roles that will yield the greatest benefit from having the BOMs in the CMMS. The storeroom benefits by;
- Knowing which parts belong to which equipment
- Ability to quickly identify obsolete parts when equipment is removed from the site.
- Ability to quickly order the part, to the right specifications
- Ability to assist the craftsman in locating the right part for the task
There are many more benefits to the team, when BOMs are enabled. The biggest benefit is for the Maintenance Planner.
How BOMs Can Expand the Efficiency of the Planner
Typically BOMs will be found within the equipment manual. When the BOMs exist only in equipment manuals, the time to locate the right assemble and part can be time consuming for the planner. The planner must identify parts for all the jobs that are performed on site, so searching through manuals is a time consuming process.
When in a CMMS, the BOMs are dramatically easier to use. The ability search them and the speed of which a part can be located is tremendous. This is one of the biggest steps a site can do to not only improve the efficiency of the planner, but also the effectiveness. The effectiveness is improved, as the likely hood of identifying the wrong is reduced with the BOMs in the CMMS. The BOM expands the efficiency of the planner by;
- Improving the ability to locate the right part
- Reducing the time to add part information to the job plan
- Reducing the time to gather the purchasing data for the storeroom
The BOM is one of the most powerful tools of the planner and is a key enabler of improving the Maintenance Planning & Scheduling process.
Do you have BOMs setup for your critical equipment? If not, what is the biggest barrier to doing so? I have worked with sites in the past that did not have a single BOM in their CMMS, now they have hundreds. How? They set a goal to first spend 1 hour a week developing BOMs and then that grew to 1 BOM per week and so on. They also build BOMs for equipment that was all over the plant. By building one, they built many. So what are you waiting for? Start small and see the improvements roll in.
Remember, to find success, you must first solve the problem, then achieve the implementation of the solution, and finally sustain winning results.
I’m James Kovacevic
HP RELIABILITY
Solve, Achieve, Sustain
Follow @HPReliability
Thanks. BOMs made it easy for in my days. It must be in sync with central stores for realistic work preparation.