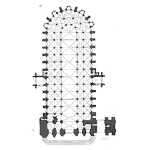
Leverage the existing data in your CMMS to make sustainable improvements to your maintenance program
Part 1 of 7
Let’s face it, your technicians have been entering data into the CMMS for years, but you haven’t been able to use it to make improvements. Is it because the data isn’t codified or it doesn’t have the right data points? Generally, this is how most maintenance managers will view their data, but it is incorrect. The CMMS does have data that you can use almost immediately.
To what extent you can use it may vary, but it will allow you to perform some level of analysis. The analysis may vary from a Weibull to a Reliability Growth Plot to a simple Pareto, but it will allow you to quantify and make improvements.
This is the first of 7 posts on the topic of Using Maintenance Data to Improve the Performance of your Manufacturing Process, with Fred Schenkelberg from FMS Reliability. Over the course of the 7 posts, we will be discussing the data, the analysis and what to do with the outcomes of the analysis to make sustainable improvements in your plant’s performance.
The Data in Your CMMS
Most CMMS’ have the data you need to perform the analysis that will make a difference. In the CMMS, you have equipment history which contains;
- What equipment was repaired or replaced
- Parts used in the repair
- Date it was repaired or replaced
- A failure cause (if you are lucky)
According to Paul Barringer’s paper on FRACAS, you need a basic amount of information to perform meaningful analysis;
- Equipment ID
- Age to Failure Data (time, hours, cycles, etc.)
- Suspended Age to Failure data (items that were removed prior to failure from Preventative or Predictive maintenance.)
- Reason for failure
When comparing these two lists, there is a clear correlation between the two. This highlights that the right information exists in your CMMS already. So why are you not using the data in the system? Most likely it is because the data needs to be extracted and may need a little cleansing prior to being used.
Extracting the Data from The CMMS
Depending on the CMMS that is utilized there are a few ways to extract the required data. If you have a well-defined failure report built, you can just use the report to get the failure data. Unfortunately, this is not the case for most organizations, so how can you extract the data?
- Export Equipment History: Use a work history report for a specific piece of equipment. This will allow you get the majority of the data required (although it may take some work to cleanse it, but that will come).
- Identify Time Period: Pull the history for a time period that covers the equipment as it is in its current operating context and since any major design changes. Why is this? If the operating context has changed, or the equipment underwent a redesign then the history may not provide an accurate representation of the failure(s) you are working to eliminate.
- Segregate Failure Modes: According to a great presentation by John Reeve, a failure mode is made up of a component, component problem and the cause of the failure. Go through the history and segregate each of the work orders in the history according to the failure mode. This is made easier if failure coding was used, but it is not required.
- Determine Age to Failure: With the work order history segregated, you can determine the age to failure by using the completed dates of the work order.
First sort the failure modes in ascending order and then use your production data (if the equipment is not run consistently) to populate the units of Age to failure in terms of hours, cycles, or days.
- Determine Which Data to Censor: There will be times when components are replaced prior to a complete functional failure due to Preventative Maintenance, or Overhauls. These activities need to be identified and can be done with a simple indicator such as an “x”.
- Sort Failure by Age to Failure: In order to run many of the analysis, you need to have the Age to Failure data in ascending order.
Comparing the outcome of extracting and cleansing the existing CMMS data to what Paul Barringer describes as the right data, you can see that the existing data has what the right data to perform the analysis.
Using the Data from the CMMS
Congratulations, you now have clean data from your CMMS which is ready to be used. You can use a variety of analysis with the data;
- Weibull: a distribution that is widely used in reliability due to its versatility and relative simplicity. Weibull distributions can be used to model a variety of life behaviors such as Early Life, Useful Life or Wear out Life. Weibull is best used for single failure modes at the component level.
- Reliability Growth Analysis: Also known as a Crow-AMSAA, is another statistical method that can be used to track changes in the reliability. It can be used with mixed failure modes at the equipment or systems level.
- Mean Cumulative Plotting: a plot over time of the cumulative failures. The plot is a simple and informative way for analyzing data on numbers or costs of repeated repairs of a sample of systems.
As you can see, you have data in your CMMS to conduct analysis and improve plant performance. Do you use the data in your CMMS? If not, have your tried to extract the data and prepare it using the guidelines in this post? It is only when we quantify our losses and use data-driven decision making, that we can develop a sustainable improvement cycle.
In the next post, Fred Schenkelberg will discuss the basics of a Weibull Analysis and how it is used to deliver benefits to your organization.
Remember, to find success, you must first solve the problem, then achieve the implementation of the solution, and finally sustain winning results.
I’m James Kovacevic
Solve, Achieve, Sustain
_
Fred Schenkelberg is an experienced reliability engineering and management consultant with his firm FMS Reliability. His passion is working with teams to create cost-effective reliability programs that solve problems, create durable and reliable products, increase customer satisfaction, and reduce warranty costs. If you enjoyed this article, consider subscribing to the ongoing series at Accendo Reliability.
All seven articles in this series in one short ebook, interested?
Please login with your site registration to download this ebook which includes all seven articles in this series.
[popup type=”” link_text=”Login” link_class=”button”]
[/popup]
If you haven’t registered, it’s free and takes only a moment.
The other articles in the series include:
Post 1 – Using the Maintenance Data You Already Have
Post 2 – The What & More Importantly, The Why of the Weibull Analysis
Post 3 – Quantify the Improvements (or Gaps) In Your Reliability
Post 4 – First Step in Analyzing Repairable Systems Data
Post 5 – The Next Step in Your Failure Data
Post 6 – The Next Step in Your Data Analysis
Post 7 – Data Q&A with Fred & James
References:
FRACAS – www.barringer1.com/pdf/SMRP-Barringer-FRACAS.pdf
Paul Barringer – http://www.barringer1.com/bio.htm
Fred Schenkelberg – accendoreliability.com/about/fred-schenkelberg/
FMS Reliability www.fmsreliability.com
Accendo Reliability accendoreliability.com/musings/
New Weibull Handbook http://geni.us/Weibull
Without Failure Data All You Have Is A Work Ticket System John Reeve https://www.linkedin.com/pulse/end-game-really-failure-data-john-reeve
Mean Cumulative Plot http://nomtbf.com/2012/02/graphical-analysis-of-repair-data/
Leave a Reply