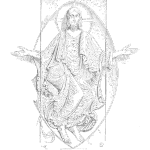
The work order report is the maintainer’s opportunity to advise the engineer what problems exist with equipment out in the plant.
It can also provide an accurate record of what was found during the repair. This makes it important that work order reports are completed in detail and are reviewed by managers and engineers.
Keywords: CMMS, computerized maintenance management system, breakdown, corrective, work order, implementation.
Reporting back on a completed work order is vital.
This task is often seen by tradesmen as a time-consuming requirement of little worth. This view is terribly wrong.
Each repair contains valuable information to improve the future performance of the equipment repaired.
But this information is only valuable if the people who can authorize money for plant improvements are alerted to a problem. The work order report is a tradesman’s opportunity to tell maintenance management the equipment problems they have to live with and what to do to solve them.
A wise maintenance engineer will read all the work order reports for his section of the plant. It gives him additional insight into the plant through other’s eyes.
If the work order is not read by middle managers in maintenance, then improvements to plant and equipment will be slow.
A good work order report tells the reader what the tradesman saw.
Such as “There were score marks around the shaft under the bearing inner race.” Indicates the inner race had probably spun and there may be too much clearance between the shaft and race or the bearing is getting hot and expanding.
This could lead to changing tolerances on drawings or investigating lubrication requirements. Another example is “The rubber in the shaft lip seal was hard and cracked.”
This may mean the temperature was too much for the seal or the wrong rubber was selected.
The tradesman’s comments are critical in the effort to continuously improve plant performance.
A good work order report also tells the reader what the tradesman did to fix the repair.
In the example of the shaft bearing “Polished bearing seat and fitted new bearing” tells the reader the problem has not been fixed and it will likely reoccur.
But – “Checked shaft tolerance and found it was undersized by 0.05mm. Machined shaft and shrunk fit a sleeve.
Machined sleeve to within tolerance and installed new bearing.” – says at least one possible problem (an undersized shaft) has probably been eliminated.
*CMMS –Computerised Maintenance Management System
Mike Sondalini – Maintenance Engineer
We (Accendo Reliability) published this article with the kind permission of Feed Forward Publishing, a subsidiary of BIN95.com
Web: trade-school.education
E-mail: info@trade-school.education
Leave a Reply