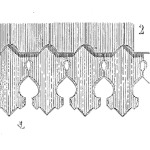
Every process should operate stably. Every process may have many measurements available to monitor either various aspects to the final product or the assembly equipment. There may be hundreds of possible items to measure and monitor.
We do not have the resources nor time to apply control chart principles to each possible measurement. Control charts do not directly add value and they have a cost to maintain and interpret. While it may be tempting to add a dozen or so control charts, as the cost increases the value quickly decreases.
How to decide what to measure
If it is not practical to measure and control chart everything that is possible, how do we decide what to measure?
In some circumstances, there is a dominant parameter that represents the key attribute of the process. In most cases, review the critical to quality elements of the process output. This may provide a basic starting point. They also represent the key process output variables (KPOVs).
One key consideration is to make the measurement as close to the process step that creates the KPOV and monitor at that point. Another consideration is to monitor inputs to the process when they have a strong correlation with the KPOV. The input variables are then key process input variables (KPIVs). The intention is to monitor elements that provide meaningful feedback to the process or provide a means to minimize scrap.
Every situation is different, yet the following may provide a guide to help you decide:
- Safety – elements that impact human or environmental safety.
- High defect rate – monitor and improve the processes to minimize defect and scrap rates.
- Customer complaints – monitor and improve process aspects to reduce complaints.
- Standards – show compliance with applicable standards.
- Customer requests – they may have an aspect of a product that impacts their results.
- Difficult processes – some setups and process operations just have more variability.
- Direct measurement – have the person charting does the measurements.
- High expenses – monitor and reduce the unwanted high costs of variability.
- Secondary variables – items that help control the process
- Incoming inspection – if the supplier is not maintaining sufficient control, these charts may provide evidence to help the vendor improve.
Start, review and adjust
When learning to control chart, look for one or more sources of measurements and practice. Just try it.
Become comfortable with the mechanics of creating a chart and interpreting the common and special causes as they occur. Always manually measure and chart before automating the process. Determine if the charted variable is worth the effort to measure first.
Then review your process and identify the KPOVs or KPIVs and establish the appropriate control charts. Collect data and regularly review that the charts are well maintained.
Periodically review the existing charts to determine if they are providing value. Does the chart actually help the process remain stable, reduce scrap, minimize costs, or what every is deemed of value for the process? If so, then continue, if not, then consider other elements of your process to monitor and improve.
Control charts once established are not like government agencies and must remain in place forever. Regular review, remove and restart charts as your process evolves and improves.
Creating/Detecting Real Control Charts
A real control chart is a living document and used regularly to make decisions to improve a process.
It is not behind glass on the wall near the entrance just for visitors. In my opinion, they should be manually done, dirty, on the line and charted by the person operating the process.
However the chart is compiled, it is real if it is used to make decisions that lead to either a stable process or an improved and stable process. Also, the variable measures should directly relate to a KPOV or KPIV – in short, the element measured should matter to the process or customer.
Related:
Selecting Control Charts (article)
Variables Control Chart Background (article)
Statistical Process Control Overview (article)
Leave a Reply