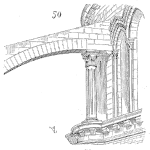
In an ideal world, our products and equipment will just work. They would not fail and would not require warranty claims, product returns, or repair.
Unfortunately, we make design mistakes, assembly errors, incur damage, or simply fail. The desired balance for most businesses is the cost of returns will not outweigh the profit of sales.
During the design process, we consider how customers will use the device, where it will be used and under what conditions. We consider the materials, assembly and shipping/installation, too. We, as providers of equipment, would like the product to work as expected for the customer.
That doesn’t always happen.
How long will this unit last?
When we assemble a specific unit and ship it to a customer, we really do not know how long that specific unit will last.
We can know.
Instead of shipping to a customer, use that unit in as real a customer situation as possible and monitor the time to failure. While this approach accurately measures the life of the product, it does not allow the customer to benefit from owning and using the device.
Another method is to wait for the customer to notice the product has failed and notify us of the problem. The customer, hopefully, has enjoyed some value from the product and has used it in an actual customer environment. We may not know when the unit was put into service or when it failed specifically, yet we generally have a pretty good idea.
Neither of these methods helps the design team while designing that specific product. Looking at product failures after they occur is too late for the initial product design process.
Is there value in a product return?
Yes, if we know how to extract that value.
Consider that most products are either part of a product family of similar products, or are part of a series of products each with minor improvements. It is increasingly rare to find a truly new product as most are built on previous designs.
The design team generally doesn’t disband after the initial design, they start work on the next generation. The team may focus on adding features or reducing cost, or something similar. Yet, the team will generally start with the just finished design.
If they follow the same process, consider the same situations, conduct product testing the same, etc. they will design a product about as reliable as the previous one.
Is that good enough?
Any product failure, during design or with a customer, provides information on what went wrong. It could be a design, assembly, use error, yet somewhere along the process, something went wrong.
The field return, with full failure analysis, may provide information on what failed. With a little work, we can estimate the conditions that caused the failure. And, therefore estimate where the most likely error occurred that led to the product failure.
Without the analysis and reflection, we lose the opportunity to learn. We ignore the decision process, the design assumptions, and the other elements that make up creating a product. which failed.
Preferably we find and correct errors that lead to field failures before shipping to customers. When this is well done, we may elect to not fix some issues as they are rare and will not cause serious harm (this does take careful consideration – think about ignition or brake pedal issues causing with major recalls).
Even if the failures occur at a customer site, it is too easy to dismiss the failure to user abuse, over-stress or some other factor considered outside the design consideration. Are we really saying the product fails and we are dismissing it as ‘not our fault’?
Look at every failure
It may be time to consider each and every failure. Evaluate the root cause which includes the material and design science, and includes the management decision making process. Consider the dynamics, objectives, rewards, and other factors that influence design decisions.
When failures occur and they are expected and well characterized then you are still learning – that your process is working.
Do you have 25% no fault found? Do you learn from each failure? Where do you find value in product returns?
Related:
Leave a Reply