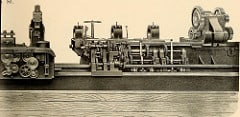
A Problem With MTBF
(Physics gets in the way!)
A Guest Post by Kevin Walker
I had an interesting case study a couple weeks ago, where “I’m giving you what you want, not what you asked for “ when the requirement as usual was a blanket MTBF, but the product design elements clearly indicated wearout could / would be a factor. — Kevin
The Scenario
- Customer RFP specified a sensor system comprised of two subsystems
Each contains some electronic components and also mechanical wear-out elements (solder fatigue, bondwires)
- Specification required MTBF of 100,000 hrs, and a Design Service Life of 10,000 hrs, also equal to 10,000 cycles
- Preliminary reliability prediction was required. System content pointed to a combination of constant and non-constant Weibull failure rate elements applying Physics of Failure
Simple block diagram created to combine both types of failure rates
Predicted result showed that the system would exceed the reliability requirement over the service life, but would not meet the specification MTBF!
Approach
A simple reliability block diagram.
Electronic components & connectors simplified to constant failure rates, and combined for each subsystem
While cycle life was relatively low (10,000) thermal cycle range was very severe so potential for solder fatigue and bond wire fatigue needed to be addressed to present an accurate representation
Life predictions done for key components, and loaded as Weibull model elements for quantity of component type used in design
Resulting predicted system reliability curve used to assess against requirements
System Reliability vs. Time
Predicted reliability will be above 100,000 MTBF until well past service life.
System Reliability vs. Time with Sub Elements
The wear-out factors create non-constant failure rate causing the total MTBF to fall below 100,000 hours.
[Fred: do the math and avoid using MTBF. Thanks Gene for the example based on a real case. If you have a case study or story to share – send it over for posting here on NoMTBF.]
Leave a Reply