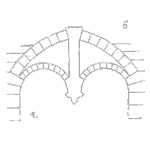
Lately, I’ve seen some evidence of reliability engineers giving up.
Throwing in the towel. Going with the flow. Not rocking the boat.
Is that our charter? To roll over and accept that we cannot make a difference?
No, it’s not.
The obstacles we all face
Not every organization is solely focused on creating reliable products or running equipment at the highest availability possible. In fact, few organizations are, in my experience.
What I have seen most often is organizations trying to create and ship products that meet customer needs. Products that solve a problem or make the customer’s life a bit easier or enjoyable.
Factories that want to create and ship products using the equipment on hand. Today’s deadlines are urgent and believed important.
We do not have enough time for accelerated testing or design of experiments, even though we all know they both actually can save us time in the long run. We don’t have time to apply the right sample size calculation, so grab a standard value.
We lack time for failure analysis and root cause investigations so we see the same problems.
The money, time, space, samples, tools, are rarely all ready to go. Even if they are, we don’t have the staff of experts to make it all work well.
We are alone.
We alone bring to the table the concerns about failures in the hands of our customers and on the plant floor. We represent bad news, caution, and tell stories of potential problems.
What can we do?
To start we can change decisions.
That is what we do. We inform, advise, cajole, and influence decisions across the organization. We do represent reliability, including the failures, yet we also represent what happens when the equipment operates reliably, or products “just work”.
You can provide insights that lead to selecting the right vendor even if it costs a tad more. If the reduction in failures outweighs the cost of purchase, it’s the right thing to do based on cost alone. And, it has the added benefit of reducing time sorting out why those parts fail.
You can present data that changes the warranty or maintenance policy. Clearly understanding the nature of failure rates allows us to manage the cost of warranty, or to determine if our maintenance program is effective or not. Just a graph of the time to failure data. It works wonders.
You can ask questions about what if it “just works”. Get others thinking beyond the cost of the parts, the time spent down for maintenance, and focus on the benefits or value of the product or equipment just working.
I’ve personally used reliability engineering tasks and results to change the focus of a development team (FMEA), avoid an expensive product recall (root cause analysis), and avoided the construction of a major factory (Weibull plot).
Some of our projects are small, some large. Some are required and some just make sense to do. With each and every reliability task you undertake, determine how it impacts the organization and customer. Find and understand the value you provide and work to make sure that value occurs.
If you want to simply fill out forms or record meaningless test results, that is your choice. I think you are missing a chance to make a difference, enjoy your work, and earn the respect you deserve.
Related:
Successful Reliability Engineers Add Value (article)
Success as a Reliability Engineer (article)
Reliability as Part of Every Decision (article)
I really like the comment in the last paragraph. I have worked with reliability engineers who are just content with filling out forms. Thus, by not using reliability toolkit are not making a difference,miserable and not enjoyinh their work and most of all not getting the respect.
We can and should make a difference – to some extent it is a personal choice. I hope by sharing what has been done or possible, that more will take on challenges and make a difference. cheers Fred
When components in a system have constant Failure Rates, Mean Time Between Failure (MTBF) of the system can be used to represent or calculate Reliability at any time within the Useful Life period. This is usually done by a Reliability Engineer
The mean life function (often denoted as “MTBF”) is not a good measurement when used as the sole reliability metric. Instead, the use of a reliability value with an associated time, along with an associated confidence level, is a more versatile and powerful metric for describing a product’s reliability
For people who are unable to establish a Failure/Time distribution to calculate reliability of their product, the easiest way to track Reliability is to use MTTF(MTBF) periodically. “Single Point” calculations are not suitable for warranty, spares allocation, etc. Should calculate the MTTF(MTBF) number at a Confidence Level.
Confidence limits for the mean are an interval estimate for the mean. Interval estimates are often desirable because the estimate of the mean varies from sample to sample. Instead of a single estimate for the mean, a confidence interval generates a lower and upper limit for the mean. The interval estimate gives an indication of how much uncertainty there is in our estimate of the true mean. The narrower the interval, the more precise is our estimate.