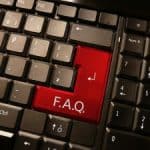
A Question & Answer Period with Fred Schenkelberg and James Kovacevic on what can be done with your data and analysis.
Data and the analyses that use the data can be tricky to manage at best, let along extremely difficult.
In this last post of the series on using the maintenance data you have, Fred and James will answer many of the common questions asked about data and the analyses.
How does one build a proper asset hierarchy? A hierarchy should be built to the recommendations in ISO 14224. This will ensure all maintenance data is recorded at the component level and can be rolled up to the highest levels of the organization.
Are all the data fields actually required? It depends entirely on the level of the analysis you are trying to do. What is required for a Weibull will vary from what is required for a mean cumulative plot. ISO 14224 covers what is ideally collected in terms of maintenance data and failure data to facilitate a reliability program.
How do I get good data from each preventative or corrective maintenance action? What data should be collected? The key to good data is to define what data is required in what format. Once the data is defined, actively audit and coach the team to provide the right data. In ISO 14224, the standard defines the difference of preventative maintenance as maintenance data and corrective maintenance as failure data.
Who should be doing the analysis, when there is no Reliability Engineer? If you don’t have a Reliability Engineer on staff, does you organization truly understand the value of the role? If not start educating the leadership team on the value and get a Reliability Engineer. If you must do the work without the role, look for someone who has a knack for stats, and likes to work through issues to develop the root cause. This could be a planner or a supervisor.
Who enters the data into the CMMS? The data is best entered by the person in the field as they perform the preventative or corrective maintenance. This will ensure accurate and timely data. Once the Root Cause Analysis has been completed, the data should be updated as needed by the Reliability Engineering.
What is a good metric to summarize the data we are gathering? Data quality can be measured a few ways; Completeness, Timeliness, Validity, Consistency, and Integrity. In reality, you need to determine what is required by the organization in its current state. For example, if you have an issue with the timeliness, use a metric that measures the time from when a work order is completed to when the data fields are populated. The metric needs to drive changes in the organization or it will not be value added.
Can a Weibull be used on a repairable system? It could be used and will provide a fitted curve, yet will not be useful to describe the data. The Weibull analysis is best for the time to the first failure (non-repairable data or restoration is always to as good as new). Instead, use a mean cumulative function plot to quickly visualize your repairable data. Another tool is the non-homogeneous Poisson process.
Can a Weibull be used with mixed failure modes? It can, but the results will be skewed. If you are using mixed failure modes, use a Crow-AMSAA or a Mean Cumulative Failure Analysis. Another approach is to separate the failures by type or failure mechanisms and analyze each mechanism separately, holding all other failure or un-failed items as right censored data.
Can a Crow-AMSAA be used with single and mixed failure modes? Absolutely it can be. The Crow-AMSAA can be used with both mixed and single failure modes. One of the greatest advantages of the Crow-AMSAA is that it can be used with mixed failure modes, trends and indicates reliability and lastly, can predict the date of the next failure.
How can I use my data to determine if my maintenance program improvements are working? No matter what you do, do not use MTBF to look for improvements. For more information on this, please read more at www.nomtbf.com. A Crow-AMSAA can be used to trend and see the improvements. For repairable systems plot the data as in a mean cumulative function plot. If the data suggests a bow upwards things are getting worse. If the bow is downward or flattening over time, then your system is getting better.
What software is available to conduct the Weibull or Crow-AMSAA Analysis? Both can be conducted in Excel, but it requires an understanding of the analysis techniques. SuperSmith and Weibull++ are two of the best programs for this.
Where can one learn more about the analyses and data in covered in these posts? There are many great references and information on these techniques. Check out the following websites:
You can also check out many of the webinars and courses available from ASQ, and SAE.
What are the go to books to learn more about this analysis and data? There are many good books on the topic and they include;
- The New Weibull Handbook
- The Basics of FMEA
- ISO 14224
- Certified Reliability Engineer Primer – Quality Council of Indiana
- Practical Reliability Engineering – Patrick P. O’Connor
- Practical Engineering, Process, and Reliability Statistics – Mark Allen
- Reliability Statistics – Robert A. Dovich
This is the last post in this series, and I want to thank Fred for sharing his vast knowledge. If there is something that we did not answer or provide insights to that you would like, please let us know by contacting us at info@eruditio.com.
Remember, to find success, you must first solve the problem, then achieve the implementation of the solution, and finally sustain winning results.
I’m James Kovacevic
Eruditio, LLC
Where Education Meets Application
_
Fred Schenkelberg is an experienced reliability engineering and management consultant with his firm FMS Reliability. His passion is working with teams to create cost-effective reliability programs that solve problems, create durable and reliable products, increase customer satisfaction, and reduce warranty costs. If you enjoyed this article, consider subscribing to the ongoing series at Accendo Reliability.
—
The other articles in the series include:
Post 1 – Using the Maintenance Data You Already Have
Post 2 – The What & More Importantly, The Why of the Weibull Analysis
Post 3 – Quantify the Improvements with a Crow-AMSAA (or RGA)
Post 4 – Using a Mean Cumulative Plot
Post 5 – The Next Step in Data
Post 6 – The Next Step in Your Data Analysis
Post 7 – Data Q&A with Fred & James
References:
Fred Schenkelberg
FMS Reliability
Accendo Reliability
New Weibull Handbook
Leave a Reply