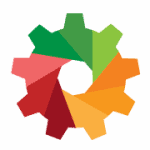
Production processes come to a grinding halt when equipment breaks down. This results in production delays, costs incurred to fix the machine, and opportunity costs. The production process cannot proceed until the maintenance activity on the faulty machine is complete — unless you have provisioned equipment redundancy.
Equipment redundancy
In industries and manufacturing facilities that require high machine availability and reliability, it is not ideal to halt production due to a machine breakdown. Multiple machines run in parallel, even if one of the machines breaks down, the production process need not be halted as other machines can take on the workload of the broken-down machine.
The technique of running multiple machines in parallel to provide availability of machines is called equipment redundancy. In the case of a machine breaking down, the remaining machines can take over the workload without any time lag. When each of the machines that run in parallel has the capability of taking over the complete workload, then the equipment is said to be fully redundant.
If an industrial application requires 2,000 W of power input from a Power Supply Unit (PSU), you can implement equipment redundancy in two ways. One option is having three machines with a power output of 1,000 W. If one of them fails, the remaining two are capable of delivering the 2,000 W required. The second way is to use three PSUs with a power output of 2,000 W each. Even if two of those fail, the third one is capable of delivering the complete power requirement. This makes this setup fully redundant. Fully redundant equipment is much more reliable than mere redundant equipment.
Redundancy, standby, and backup
Redundancy, standby, and back up all help in improving the availability and reliability of machines. But all three terms do not represent the same concept. There are slight operational differences between them.
In equipment redundancy, all pieces of equipment are operational in parallel. When one machine breaks down, the remaining operational ones take over the load of the broken-down one instantaneously. But standby equipment and backup equipment do not work in parallel.
With standby equipment, when the main machine fails, the one on standby takes over the workload. It does not work in parallel with the main machine, but is ready to take over the load instantaneously when the main piece of equipment fails. In the case of backup equipment, it is not readily available to take over the workload of failed equipment. Backup equipment is usually in storage and it has to be brought operational when the main machine fails.
Pros and cons
Equipment redundancy is one of the prominent techniques for improving the availability and reliability of equipment in a facility. While that is an advantage, there are many more benefits and costs to implementing equipment redundancy.
Pros
- Higher machine reliability is possible with equipment redundancy.
- Maintenance becomes easier with equipment redundancy as there is no emergency to get the failed equipment back online. The production process is not halted, giving the maintenance team breathing room to properly work on the failed device.
- Equipment redundancy is a simple technique to improve the reliability of equipment. Since complex reliability techniques are not used, there are fewer chances of things going wrong.
Cons:
- High capital expenditure has to be incurred for equipment redundancy. Multiple pieces of equipment have to be brought instead of one.
- Equipment redundancy increases the complexity of operations. It is the easiest method for improving reliability, but it is not the simplest in terms of operations. Operating single machines without redundancy is much simpler.
- Multiple machines have to be regularly maintained and have their parts replaced, increasing the operational costs with machine redundancy.
- Increased regular testing is needed to ensure equipment redundancy works as expected.
- Equipment redundancy instills complacency in operations and maintenance teams to improve the reliability of individual equipment.
Redundancy for system reliability
Reliability engineering is a vast field with multiple potent techniques to improve machine availability and reliability.
Equipment redundancy is one of the most simple techniques of reliability engineering. It improves reliability, as operations will not be hindered even if a machine breaks down. However, as we have seen, equipment redundancy is costly.
The decision to rely on equipment redundancy has to be based on multiple different factors. The critical nature of the equipment is a major factor in determining the need for redundancy.
Sometimes, other reliability engineering techniques are better at improving reliability at a fraction of the cost. Alternatives have to be explored before deciding to go down the redundancy route to improve machine reliability.
In some instances, there is no alternative to improving reliability without redundancy. In such cases, redundancy is essential. In all other instances, cost-benefit analysis, return on investment, and cost of not having redundancy have to be favorable to go ahead with equipment redundancy.
Leave a Reply