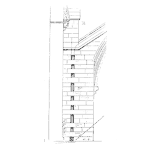
Behind all lasting business success is the ability to make business processes work successfully. Random success in business is due to luck. But lasting success relies on knowing how to use statistical process control to make your processes more successful more often.
Keywords: statistical process control (SPC) business process management (BPM)
The email query below is the latest of many similar ones that I get each year.
I am coming to Operations M&R from the world of Projects Planning/Scheduling, and have NO plant operational experience. My goal is to become a world-class Maintenance Planner.
Grateful for your advice as to an appropriate order for your online training courses.
Was thinking:
1. EAM – The Plant Wellness Way: for an initial overview/grounding
2. Maintenance Planning & Scheduling for Reliability
Not sure when/whether to take:
1. Preventive Maintenance Strategy
2. Predictive Maintenance Strategy
Thank you very much in advance.
My reply is below.
Congratulations on the career move. I’ve always found M&R to be a fascinating, challenging and demanding field of business.
Now some tough news. Unless you can personally rebuild the machinery or equipment you maintain, and explain how to do that correctly to other maintainers, you can never be a great maintenance planner. Have you seen do-it-yourself car maintenance manuals written for car owners who do their own maintenance? A maintenance planner has to be able to write the complete “car maintenance manual” for their machinery and equipment. You need to know the plant and equipment so well that you can write the manual that all its maintainers will use in future. World class mechanical, instrumentation or electrical maintenance planners need to be that good.
That does not preclude you from taking a maintenance planning and scheduling (MPS) job, but you need to address how you will properly do the maintenance planning functions. I tell people who don’t know their plant and equipment’s engineering and cannot do maintenance and repair of real machines and production equipment to use the best maintainers in the crew to write the procedures and identify the needed parts. It’s not the right thing to do, but it’s all that is left to you to do. Scheduling is not so demanding on plant and equipment knowledge, and persons with a strong project management background like you will master maintenance scheduling quickly.
I suggest you do the MPS course first. Its certificate level coverage gives you a good overview, important process knowledge and useful insights into the MPS functions you need to handle.
A company that gives critically important jobs to people without the capability to do their roles masterly will ruin the statistical process control of their business.
Managers and Supervisors are in charge of making their business processes ever more successful. Ultimate process control means all causes of randomness are limited to what brings sure success. When a manager or supervisor makes decisions that increase process randomness it is a sure tell-tale sign that they don’t understand statistical process control or business process management.
You want robust, stable processes whose design and operation naturally deliver successful results every time they are used. You “see” how successfully a process is performing by charting its degree of statistical stability. Knowing what impacts, changes and improves the statistical process control performance of your business processes is a critical requirement for a manager’s personal career success and for their company’s long term survival.
The vital importance of thorough maintenance planning and project planning has been identified by many organizations. Articles and white papers related to the benefits of planning identify it brings valuable business benefits such as cost reduction, greater safety, higher productivity, improved resource coordination, reduction in manpower, fewer mistakes and repeat work, on time completion, along with other consequential advantages. Very few people realize those benefits are the results of the business process design they use.
Giving the maintenance planning job to a person who cannot personally maintain the equipment they are planning work for prevents maintenance process success. A maintenance planner must select and write the step by step instructions of how to do every task in a maintenance job. Only people who know and understand the equipment design, its engineering, and its risks and dangers can do that level of expert planning and job preparation. Our unlucky novice “planner” is starting a new role where they can never be a truly successful maintenance planner because they only can do project planning and know nothing about the detailed engineering and construction of the production plant and equipment whose maintenance they must plan for in great detail. They have never gained the tactile and sensory knowledge, task skills and risk awareness you need to know when you plan and prepare maintenance activities.
When people are given jobs that they cannot do properly the process capability to cause the intended process outcomes is destroyed. To get more effective maintenance planning and execution you must lift the process’ capability to get the results that you want. The manager who approved our novice maintenance planner to do a maintenance process role they can never do well introduced many future workplace problems, guaranteed that confusion reigns, gave distress to the incumbent, and brought endless plant and equipment failures into their company.
Our new incumbent will have years of unhappiness as a maintenance planner because they can never master their job. So too will unhappiness come to their manager, to the maintenance crew, and to the operations group. The manager unintentionally brought pain and sadness to the business because they did not understand how to make their organization more successful through the correct use of statistical process control in business process management. Every manager and supervisor who does not understand SPC and its proper use in business process behaviour management and process improvement dooms their organization and themselves to the fates of random luck.
All the best to you,
Mike Sondalini
Director
www.lifetime-reliability.com.au
Leave a Reply