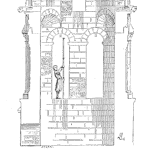
One of the most challenging aspects of being a consultant is addressing the musings of those who have accepted defeat.
With a smile of course; and friendly reassurance that you have in fact worked with companies who were worse off and with some training, confidence and a sound business plan they were able to turn things around to a point where people actually enjoyed coming to work.
Having stated this, I still have a list of my excuses as to why someone thinks we are “wasting our time” as we work to improve the reliability of their assets.
- “We tried that (PdM, RCM, RCA, Lean Manufacturing, TPM, Operator Care) it don’t work here.” While I could provide hundreds of examples where each of these tool has worked, the one thing they all have in common is someone stepped up to lead. Leaders don’t have to be executives, managers, engineers or supervisors; just someone who believes in the tool and has the drive and ability to create and prove a business case for change.
- “That won’t work here, we are different” Having worked in nearly every type of industry over the past 30 years I have to say this excuse might be my all-time favorite. From harsh environments with severe corrosion and erosion to clean rooms where even the slightest amount of contamination can ruin millions of dollars of product, the only thing that makes some companies different is they have accepted defeat. They have given up on continuous improvement and have made the decision to live with the failures their reoccurring and often preventable failures. If this is truly your mindset you had better hope your competitors feel the same way and I can assure you, they don’t.
- “Our Management says they support reliability but they don’t” When I hear this I rarely doubt that it’s not true. I have worked for managers who would have made great politicians because every time their lips moved they were lying. My favorite was a guy we called Bobble Head Bob, if a consultant was in the room describing the benefits of any given improvement tool, Bob’s head would be bobbing up and down in full support. As soon as the consultant left he would do his best to block any change. At the same time we continued to what we believed to be right. Continue to learn; measure, build that business plan, implement change and show results. When you improve equipment reliability and lower maintenance costs sooner or later event the doubters will want to know how you did it. The truth is managers who don’t support these efforts haven’t taken the time to educate themselves and understand why they work.
- “We don’t have enough people to make this work” With the present condition of your plant and your current level of emergency and demand maintenance maybe you don’t. The reality in most cases is you have enough people; they just aren’t focused on the right things. While this issue takes a bit more vision, work and determination to work out of than the previous three it’s not impossible. Start with good benchmarking exercise (World Class Reliability Benchmarking) and learn where you need to focus your efforts and to ensure you are properly staffed to achieve your goals.
- “We tried that before, it doesn’t work.” Yep, I get it! The average child tries to walk and fails well over 100 times yet I didn’t see anyone crawl into the room today. Thomas Edison failed over 1000 times before he viewed the light bulb as a success. Again, success depends on people who believe the tools of our profession work, people who attend courses, go to conferences and read everything they can get their hands on to better understand what it takes to improve reliability. People like Thomas Edison who learn from their failures, identify what may have gone wrong and forge on to improve.
In closing, I would be remiss if I didn’t say the change in culture it takes to drive a continuous improvement effort is never easy. This being said, they are also not impossible. If you recognize the need for change in your business and begin to develop a plan for change, do yourself a favor and find mentor to help guide you and shorten the cycle. The best candidate would be someone with a proven track record in a non-competing business who has been there, done that and recognized the rewards.
Great leaders believe in their goals, they develop business plans, publish results, celebrate success, learn from failures, seek advice and guidance from others but trait of a great leader is they no longer tolerate excuses!
For those who may be wondering, Bobble Head Bob was in fact a former manager of mine in the earliest part of my career. For those of us who worked for him the stories we share have become a source of entertainment when we get together and talk about old times. One his more famous quotes “This digital photography thing will never take off, it’s too complicated, the equipment costs too much money and the pictures are grainy.” A true visionary!
Everyone at some point in their career if they haven’t already will work for a Bob, at that time in my career I was also lucky enough to have worked with a couple of other great leaders and managers who advised me the most important thing to remember in life is you can learn from everyone you work with. Some will teach you how to do things right and others can teach you what not to do. While he wasn’t the best he was far from the worst but most important, we all learned.
Leave a Reply